前 言
JB/T4730.1—4730.6—2005《承压设备无损检测》分为六个部分:
——第1部分:通用要求;
——第2部分:射线检测;
——第3部分:超声检测;
——第4部分:磁粉检测;
——第5部分:渗透检测;
——第6部分:涡流检测。
本部分为JB/T4730.1—4730.6—2005的第3部分:超声检测。本部分主要根据国内多年的研究成果和应用经验,参考ASTM《锅炉压力容器规范》第V卷和JIS标准规范以及行业反馈意见进行修订。本部分与JB4730—1994相比主要变化如下:
1、对壁厚小于3倍近场区工件材质衰减系数公式进行修正;增加了奥氏体不锈钢和双相不锈钢板、铝及铝合金板材、钛及钛合金板材超声检测内容;统一了爆炸和轧制复合钢板超声检测内容。
2、将钢制承压设备对接焊接接头超声检测范围扩大到6mm—400mm,对对接焊接接头超声检测试块进行了局部调整;增加了钢制承压设备对接焊接接头超声检测等级分类的内容;增加了T型烘干焊接接头以及奥氏体不锈钢承压对接接头的超声检测内容。
3、增加了壁厚大于或等于4mm,外径为32mm-159mm或壁厚为4mm-6mm,外径大于或等于159mm的钢制承压设备管子,压力管道环向对接接头超声检测内容;增加了壁厚大于或等于5mm,外径为80 mm -159 mm或壁厚为5 mm -8 mm,外径大于或等于159 mm的铝及铝合金环向对接焊接接头超声检测内容。
4、增加了在用承压设备超声检测内容。
本部分附录A至附录L为规范性附录;附录M、附录N为资料性附录。
本部分由全国锅炉压力容器标准化技术委员会(SAC/TC 262)提出。
本部分由全国锅炉压力容器标准化技术委员会(SAC/TC 262)归口。
本部分主要起草人:袁榕、姚志忠、康纪黔、阎长周、肖家伟、许遵言、潘荣宝、陈程玉。
承压设备无损检测
第3部分:超声检测
3 一般要求
3.1 超声检测人员
超声检测人员的一般要求应符合JB/T4730.1的有关规定。
3.2 检测设备
3.2.1 超声检测设备均应具有产品质量合格证或合格和证明文件。
3.2.2 探伤仪、探头和系统性能
3.2.2.1 探伤仪
采用A型脉冲反射式超声波探伤仪,其工件频率范围为0.5-10MHz,仪器至少在荧光屏满刻度的80%范围内呈线性显示。探伤仪应具有80dB以上的连续可调衰减器,步进级每档不大于2dB,其精度为任意相邻12dB误差在±1dB以内,最大累计误差不超过1dB。水平线性误差不大于1%,垂直线性误差不大于5%。其余指标应符合JB/T10061的规定。
3.2.2.2 探头
3.2.2.2.1 晶片面积一般不应大于500mm²,且任一边长原则上不大于25mm。
3.2.2.2.2 单斜探头声束轴线水平偏离角不应大于2º,主声束垂直方向不应有明显的双峰。
3.2.2.3 超声探伤仪和探头的系统性能
3.2.2.3.1 在达到所探工件的最大检测声程时,其有效灵敏度余量应不小于10dB。
3.2.2.3.2 仪器和探头的组合频率与公称频率误差不得大于±10%。
3.2.2.3.3 仪器和直探头组合的始脉冲宽度(在基准灵敏度下):对于频率为5MHz的探头,其占宽不得大于10mm;对于频率为2.5MHz的探头,其占宽不得大于15mm。
3.2.2.3.4 直探头的远场分辨力应不小于30dB,斜探头的远场分辨力应不小于6dB。
3.2.2.3.5 仪器和探头的系统性能应按 JB/T9214和JB/T10062的规定进行测试。
3.3 超声检测一般方法
3.3.1 检测准备
3.3.1.1 承压设备的制造、安装和在用检验中,超声检测的检测时机及抽检率的选择等应按相关法规、标准及有关技术文件的规定。
3.3.1.2 所确定检测面应保证工件被检部分均能得到充分检查。
3.3.1.3 焊缝的表面质量应经外观检测合格。所有影响超声检测的锈蚀、飞溅和污物等都应予以清除,其表面粗糙度应符合检测要求。表面的不规则状态不得影响检测结果的正确性和完整性,否则应做适当的处理。
3.3.2 扫查复盖率
为确保检测时超声声束能扫查到工件的整个被检区域,探头的每次扫查复盖率应大于探头直径的15%。
3.3.3 探头的移动速度
探头的扫查速度不应超过150mm/s。当采用自动报警装置扫查时,不受此限。
3.3.4 扫查灵敏度
扫查灵敏度通常不低于基准灵敏度。
3.3.5 耦合剂
应采用透声性好,且不损伤检测表面的耦合剂,如机油、浆糊、甘油和水等。
3.3.6 灵敏度补偿
a)、耦合补偿
在检测和缺陷定量时,应对由表面粗糙度引起的耦合损失进行补偿。
b)、衰减补偿
在检测和缺陷定量时,应对材质衰减引起的检测灵敏度下降和缺陷定量误差进行补偿。
c)、曲面补偿
对于探测面是曲面的工件,应采用曲率半径与工件相同或相近的试块,通过对比试验进行曲率补偿。
3.4 系统校准和复核
3.4.1 一般要求
系统校准应在标准试块上进行,校准中应使探头主声束垂直对准反射体的反射面,以获得稳定的和最大的反射信号。
3.4.2 仪器校准
每隔三个月至少对仪器的水平线性和垂直线性进行一次测定,测定方法按JB/T10061的规定。
3.4.3 新购探头测定
新购探头应有探头性能参数说明书,新探头使用前应进行前沿距离、K值、主声束偏离、灵敏度余量和分辨力等参数的测定。测定应按JB/T10062的有关规定进行,并满足其要求。
3.4.4 检测前仪器和探头系统测定
3.4.4.1 使用仪器—— 斜探头系统,检测前应测定前沿距离、K值和主声束偏离,调节或复核扫描量程和扫查灵敏度。
3.4.4.2 使用仪器——直探头系统,检测前应测定始脉冲宽度、灵敏度余量和分辨力,调节或复核扫描量程和扫查灵敏度。
3.4.5 检测过程中仪器和探头系统的复核
遇有下述情况应对系统进行复核:
a)、校准后的探头、耦合剂和仪器调节旋纽发生改变时;
b)、检测者怀疑灵敏度有变化时;
c)、连续工作4小时以上时;
d)、工作结束时。
3.4.6 检测结束前仪器和探头系统的复核
a)、每次检测结束前,应对扫描量程进行复核。如果任意一点在扫描线上的偏移超过扫描读数的10%,则扫描量程应重新调整,并对上一次复核以来所有的检测部位进行复核。
b)、每次检测结束前,应对扫查灵敏度进行复核。一般对距离——波幅曲线的校核不应少于3点。如曲线上任何一点幅度下降2 dB,则应对上一次复核以来所有的检测结果进行复检;如幅度上升2 dB,则应对所的的记录信号进行重新评定。
3.4.7 校准、复核的有关注意事项
校准、复核和对仪器进行线性检测时,任何影响仪器线性的控制器(如抑制或滤波开关等)都应放在“关”的位置或处于最低水平上。
3.5 试块
3.5.1 标准试块
3.5.1.1 标准试块是指本部分规定的用于仪器探头系统性能校准和检测校准的试块,本部分采用的标准试块有:
a)、钢板用标准试块:CBI、CBII;
b)、锻件用标准试块:CSI、CSII、CSIII;
c)、焊接接头用标准试块:CSK-IA、CSK-IIA、CSK-IIIA、CSK-IVA。
3.5.1.2 标准试块应采用与被检工件声学性能相同或近似的材料制成。该材料用直探头检测时,不得有大于或等于Φ2mm平底孔当量直径的缺陷。
3.5.1.3 标准试块尺寸精度应符合本部分的要求,并应经计量部门检定合格。
3.5.1.4 标准试块的其他制造要求应符合JB/T10063和JB/T7913的规定。
3.5.2 对比试块
3.5.2.1 对比试块是指用于检测校准的试块。
3.5.2.2 对比试块的外形尺寸应能代表被检工件的特征,试块厚度应与被检工件的厚度相对应。如果涉及到两种或两种以上不同厚度部件焊接接头的检测,试块的厚度应由其最大厚度来确定。
3.5.2.3 对比试块反射体的形状、尺寸和数量应符合本部分的规定。
4 承压设备用原材料、零部件的超声检测和质量分级
4.1 承压设备用钢板超声检测和质量分级
4.1.1 范围
本条适用于板厚为6mm-250mm的碳素钢、低合金钢制承压设备用板材的超声检测和质量分级。
奥氏体钢板材、镍及镍合金板材以及双相不锈钢板材的超声检测也可参照本章执行。
4.1.2 探头选用
4.1.2.1 探头选用应按表1的规定进行。
表1 承压设备用板材超声检测探头选用
板厚mm |
采用探头 |
公称频率MHz |
探头晶片尺寸 |
6-20 |
双晶直探头 |
5 |
晶片面积不小于150mm² |
>20-40 |
单晶直探头 |
5 |
Φ14mm -Φ20mm |
>40-250 |
单晶直探头 |
2.5 |
Φ20mm-Φ25mm |
4.1.2.2 双晶直探头性能应符合附录A(规范性附录)的要求。
4.1.3 标准试块
4.1.3.1 用双晶直探头检测厚度不大于20 mm的钢板时,采用如图1所示的CBI标准试块。
4.1.3.2 用单直探头检测厚度大于20 mm的钢板时,CSII 标准试块应符合图2和表2的规定。试块厚度应与被检钢板厚度相近。如经合同双方协商同意,也可采用双晶直探头进行检测。
图1 CBI标准试块
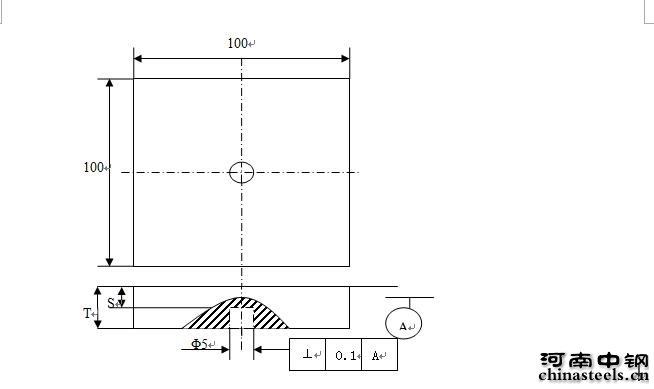
图2 CBII标准试块
表2 CBII标准试块
试块编号 |
被检钢板厚度 |
检测面到平底孔的距离S |
试样厚度T |
CBII -1 |
>20-40 |
15 |
≥20 |
CBII -2 |
>40-60 |
30 |
≥40 |
CBII -3 |
>60-100 |
50 |
≥65 |
CBII -4 |
>100-160 |
90 |
≥110 |
CBII -5 |
>160-200 |
140 |
≥170 |
CBII -6 |
>200-250 |
190 |
≥220 |
4.1.4 基准灵敏度
4.1.4.1 板厚不大于20mm时,用CBII试块将工件等厚度部位第一次底波高度调整到满刻度的50%,再提高10 dB作为检测灵敏度。
4.1.4.2 板厚大于20mm时,应将CBII试块Φ5平底孔第一次反射波高调整到满刻度的50%作为检测灵敏度。
4.1.4.3 板厚不小于探头的3倍近场区时,也可取钢板无缺陷的完好部位的第一次底波来校准灵敏度,其结果应与4.1.4.2条的要求相一致。
4.1.5 检测方法
4.1.5.1 检测面
可选钢板的任一轧制表面进行检测。若检测人员认为需要或设计上有要求时,也可选钢板的上、下两轧制表面分别进行检测。
4.1.5.2 耦合方式
耦合方式可采用直接接触法或液浸法。
4.1.5.3 扫查方式
a)、探头沿垂直于于压延方向,间距不大于100mm的平等线进行扫查。在钢板剖口预定线两侧各50mm(当板厚超过100mm时,以板厚的一半为准)内应作100%扫查,扫查示意图如图3。
图3 探头扫查示意图
b)、根据合同、技术协议书或图样的要求,也可进行其它形式的扫查。
4.1.6 缺陷的测定与记录
4.1.6.1 在检测过程中,发现下列三种情况之一者即作为缺陷:
a)、缺陷第一次反射波(F1)波高大于或等于满刻度的50%,即F1≥50%。
b)、当底面第一次反射波(B1)波高未达到满刻度时,缺陷第一次反射波(F1)波高与底面第一次反射波(B1)波高之比大于或等于50%,即B1<100%,而F1/B1≥50%。
c)、底面第一次反射波(B1)波高低于满刻度的50%,即B1<50%。
4.1.6.2 缺陷的边界或指示长度的测定方法
a)、检验出缺陷后,应在它的周围继续进行检验,以确定缺陷的范围。
b)、用双晶片探头确定缺陷的边界或指示长度时,探头的移动方向应与探头的隔声层相垂直,并使缺陷波下降到基准灵敏度条件下荧光屏满刻度的25%或使缺陷第一次反射波高与底面第一次反射波高之比为50%。此时,探头中心的移动距离即为缺陷的指示长度,探头中心点即为缺陷的边界点。两种方法测得的结果以较严重者为准。
c)、用单直探头确定缺陷边界或指示长度时,移动探头。使缺陷第一次反射波波高下降到基准灵敏度条件下荧光屏满刻度的25%或使缺陷第一次反射波波高与底面第一次反射波高为50%。此时,探头中心移动距离即为缺陷的指示长度,探头中心即为缺陷的边界点。两种方法测得的结果以较严重者为准。
d)、确定4.1.6.1 c中缺陷的边界范围或指示长度时,移动探头(单直探头或双直探头)使底面第一次反射波升高到荧光屏满刻度的50%。此时探头中心移动距离即为缺陷的指示长度,探头中心点即为缺陷的边界点。
e)、当板厚较薄,确需采用第二次缺陷波和第二次底波来评定缺陷时,基准备就绪灵敏度应以相应的第二次反射波来校准。
4.1.7 缺陷的评定规则
单个缺陷按其指示的最大长度作为该缺陷的指示长度,若单个缺陷的指示长度小于40 mm时,可不作记录。
4.1.7.2 单个缺陷指示面积的评定规则
a)、一个缺陷按其指示的面积作为该缺陷的单个缺陷的单个指示面积。
b)、多个缺陷其相邻间距小于100mm或间距小于相邻小缺陷的指示长度(取其较大值)时,以各缺陷面积之和作为单个缺陷指示面积。
c)、指示面积不计的单个缺陷见表3。
表3 钢板质量分级
等级 |
单个缺陷的指示长度mm |
单个缺陷的指示面积cm² |
在任一1 m×1 m检验面积内存在的缺陷面积百分比/% |
以下单个缺陷指示面积不记/ cm² |
I |
<80 |
<25 |
≤3 |
<9 |
II |
<100 |
<50 |
≤5 |
<15 |
III |
<120 |
<100 |
≤10 |
<25 |
IV |
<150 |
<100 |
≤10 |
<25 |
V |
超过IV级者 |
4.1.7.3 缺陷面积百分比的评定规则
4.1.7.4 在任1m×1m检测面积内,按缺陷面积所占的百分比来确定。如钢板面积小于1m×1m,可按比例折算。
4.1.8 钢板质量分级
4.1.8.1 钢板质量分级见表3。
4.1.8.2 在坡口预定线两侧各50mm(板厚大于100mm时,以板厚的一半为准)内,缺陷的指示长度大于或等于50mm时,应评为V级。
4.1.8.3 在检测过程中,检测人员如确认钢板中有白点、裂纹等危害性缺陷存在时,应评为V级。
4.1.9 横波检测
4.1.9.1 在检测过程中对缺陷有疑问或合同双方技术协议中有规定时,可采用横波检测。
4.1.9.2 钢板横波检测应按附录B(规范性附录)进行。
8 超声检测报告
超声检测报告至少应包括以下内容:
a)、委托单位;
b)、被检工件:名称、编号、规格、材质、坡口型式、焊接方法和热处理状态;
c)、检测设备:探伤仪、探头、试块;
d)、检测规范:技术等级、探头K值、探头频率、检测面和检测灵敏;
e)、检测部位及缺陷的类型、尺寸、位置和分布的应在草图上予以标明,如有因几何开关限制而检测不到的部位,也应加以说明;
f)、检测结果及质量分级、检测标准名称和验收等级;
g)、检测人员和责任人员签字及其技术资格;
h)、检测日期。
附录A
(规范性附录)
双晶片直探头性能要求
A1 距离—波幅特性曲线
采用本部分图2试块,在各个厚度上测定其回波高度(dB),作出如图A1所示的特性曲线,该特性曲线必须满足下述条件:
a、 在厚度19mm上的回波高度,与最大回波高度差应在3dB~-6dB的范围内。
b 、 在厚度3mm上的回波高度,与最大回波高度差应在3dB~-6dB的范围内。
A2 表面回波高度
直接接触法测得的表面回波高度,应比最大回波高度低40dB以上。
A3 检出灵敏度
移动探头对准图A-2试块ф5.6mm平底孔,其回波高度与最大回波高度差应在-10dB±2dB的范围内。
A4 有效波束宽度
对准图A-2试块ф5.6mm平底孔,与声波分割面平行地移动探头,按6 dB法测定波束宽度,对于承压设备用的钢板检测,其有效值应大于16mm。

图A-1 双晶直探头距离—波幅特性曲线
图 A-2 测定仪器和探头组合性能试样
附录B
(规范性附录)
承压设备用钢板超声横波检测
B.1 范围
本附录规定了用斜探头(横波)检测钢板中非夹层性缺陷的超声检测方法,并将其作为直探头检测的补充。
B.2 检测装置
B.2.1 原则上选用K1斜探头,圆晶片直径应在13 mm -25 mm之间,方晶片面积应不小于200 mm²。如有特殊需要也可选用其他尺寸和K值的探头。
B.2.2 检测频率为2MHz-5MHz。
B.3 对比试块
B.3.1 对比试块用钢板应与被检钢板厚度相同,声学特性相同或相似。
B.3.2 对比试块上的人工缺陷反射体为V形槽,角度为60º,槽深为板厚的3%,槽的长度至少为25 mm。
B.3.3 对比试块的尺寸、V形槽位置应符合图B.1的规定。
图B.1 对比试块
B.3.4 对于厚度超过50 mm的钢板,要在钢板的底面加工第二个如B.3.3所述的校准槽。
B.4 基准灵敏度的确定
B.4.1 厚度小于或等于50 mm的钢板
B.4.1.1 把探头置于试块有槽的一面,使声束对准槽的宽边,找出第一个全跨距反射的最大波幅,调整仪器,使该反射波的最大波幅为满刻度的80%,在荧光屏上记录下该信号的位置。
B.4.1.2 移动探头,得到第二个全跨距信号,并找出信号最大反射波幅,记下这一信号幅值点在荧光屏的位置,将荧光屏上这两个槽反射信号幅值点连成一直线,此线即为距离——波幅曲线。
B.4.2 厚度大于50 mm至150 mm的钢板
B.4.2.1 将探头声束对准试块背面的槽,并找出第一个1/2跨距反射的最大波幅。调节仪器,使反射波幅为满刻度的80%,在荧光屏上记下这个信号的位置。不改变仪器调整状态,在3/2跨距上重复该项操作。
B.4.2.2 不改变化仪器调整状态,把探头再次置于试块表面,使波束对准试块表面上的槽,并找出全跨距最大反射波的位置。在荧光屏上记下这一幅值点。
B.4.2.3 在荧光屏上将B.4.2.1和B.4.2.2所确定的点相连接,此线即为距离——波幅曲线。
B.4.3 厚度大于150 mm至250 mm的钢板
B.4.3.1 把探头置于试块表面,使声束对准试块底面上的切槽,并找出第一个1/2跨距反射的最大幅度位置。调节仪器,使这一反射波为荧光屏满刻度的80%,在荧光屏上记下这个幅值点。
B.4.3.2 不改变仪器的调整状态,把探头再次置于试块表面,以全跨距对准切槽获得最大反射,在荧光屏上记下这个幅值点。
B.4.3.3 在荧光屏上将B.4.3.1和B.4.3.2所确定的点连成一直线,此线即为距离——波幅曲线。
B.5 扫查方法
B.5.1 在钢板的轧制面上以垂直和平行于钢板主要压延方向的格子线进行扫查,格子线中心距为200 mm。
B.5.2 当发现缺陷信号时,移动探头使之能在荧光屏上得到最大反射。
B.5.3 对于波幅等于或超过距离——波幅曲线的缺陷显示,应记录其位置,并移动探头使波幅降到满刻度的25%来测量长度。对于波幅低于距离—波幅曲线的缺陷,当指示长度较长时,也可记录备案。
B.5.4 在每一个记录缺陷位置上,应以记录缺陷中心起,在200mm×200 mm的区域作100%检测。
B.6 验收标准
等于或超过距离——波幅曲线的任何缺陷信号均应认为是不合格的。但是以纵波方法作辅助检测时,若发现缺陷性质是分层类的,则应按纵波检测的规定处理。
中华人民共和国国家标准
GB/T2970-2004
厚 钢 板 超 声 波 检 验 方 法
前 言
本标准代替GB / T 2970-1991《中厚钢板超声波检验方法》。
本标准与GB / T 2970-1991相比,主要变化如下:
——本标准适用范围也可以包括奥氏体不锈钢板;
——双晶片直探头可探厚度范围由原20mm扩大到60mm;
——自动检验用试样有较大简化;
——双晶直探头性能要求有所改变;
——对钢板中不允许存在的单个的缺陷的要求有所提高。
本标准附录A为规范性附录。
本标准由是国钢铁工业协会提出。
本标准由全国钢标准化技术委员会归口。
本标准起草单位:钢铁研究总院,冶金工业信息标准研究院。
本标准主要起草人:张广纯、张建卫、范弘、贾慧明、黄颖、董莉。
本标准所代替的历次版本发布情况为:
——GB 2970-1982、GB 2970-1991。
厚 钢 板 超 声 波 检 验 方 法
1 范围
本标准规定了厚钢板超声波检验对比试样、检验仪器和设备、检验条件与方法、缺陷的测定与评定、钢板的质量分级、检验报告等内容。
本标准适用范围于厚度不小于6 mm的锅炉、压力容器、桥梁、建筑、造船、钢结构、管线、模具等用途钢板的超声波检验。奥氏体不锈钢板也可参照本标准。
2 规范性引用文件
下列文件中的条款通过本标准的引用而成为本标准的条款。凡是注日期的引用文件,其随后所有的修改单(不包括勘误的内容)或修订版均不适用于本标准,然而,鼓励根据本标准达成协议的各方研究是否可使用这些文件的最新版本。凡是不注日期的引用文件,其最新版本适用于本标准。
GB / T 8651 金属板材超声波探伤方法
GB / T 12604.1 无损检测术语 超声检测
JB / T 1006 A型脉冲反射式超声波探伤仪通用技术条件
JB 4730—1994 压力容器无损检测
3 一般要求
3.1 被检板材表面应平整、光滑、厚度均匀,不应有液滴、油污、腐蚀和其他污物。
3.2 被检板材的金相组织不应在检验时产生影响检验的干扰回波。
3.3 检验场地应避开强光、强磁场、强振动、腐蚀性气体、严重粉尘等影响超声波探伤仪稳定性或检验人员可靠观察的因素。
3.4 从事钢板超声波检验人员应经过培训,并取得权威部门认可的超声探伤专业I级及其以上资格证书。签发探伤报告者应获得权威部门认可的超声探伤专业II级及其以上资格证书。
3.5 检验方式可采用手工的接触法、液浸法(包括局部液浸法和压电探头或电磁超声探头的自动检验法)。
3.6 所采用的超声波型可为纵波、横波和板波。
4 对比试样
4.1 对比试样材质、声学性能应与被检验钢板相同或相似,并应保证内部不存在影响检验的缺陷。
4.2 用双晶直探头检验厚度不大于60mm的钢板时,所用对比试样如图1所示。
4.3 用单晶片直探头检验钢板时,对比试样应符合图2、表1和表2的规定。
4.4 用压电或电磁超声自动超声检验方法时,试样长边应平行于压延方向,端面应平直,厚度公差应小于板厚2%。人工缺陷的位置如图3所示。
4.5 采用板波、横波检验的对比试样形式见GB / T 8651和JB 4730-1994附录H。
注:垂直度а随试块厚度变化见表2。
图2 单晶直探头检验用对比试样
表1 单晶片直探头用对比试样
试块编号 |
被检验钢板厚度 |
检验面到平底孔的距离S |
试样厚度Y |
1 |
>13-20 |
7 |
≥15 |
2 |
>20-40 |
15 |
≥20 |
3 |
>40-60 |
30 |
≥40 |
4 |
>60-100 |
50 |
≥65 |
5 |
>100-160 |
90 |
≥110 |
6 |
>160-200 |
140 |
≥170 |
表2 垂直度а随试样厚度变化
试样厚度 |
>20-40 |
>40-60 |
>60-100 |
>100-160 |
>160-200 |
>200 |
a |
0.15 |
0.20 |
0.25 |
0.30 |
0.40 |
0.55 |






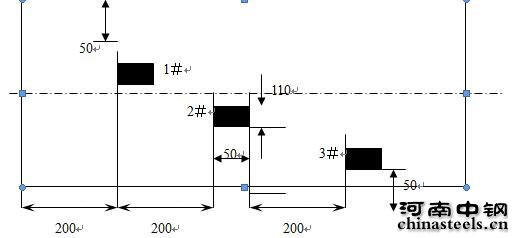
钢板压延方向
注 1:1﹟、2﹟人工缺陷为人工平底槽,加云母焊合,埋藏深度为板厚的1/2,缺陷自身高度为0mm~0.3mm;3﹟为表面铣槽(槽深为3 mm);
注 2: 1﹟、2﹟、3﹟人工缺陷的长×宽为50 mm ×10mm;
注 3:根据探伤模式的不同,可在适当位置增加适当数量直径为5 mm的当量平底孔(孔深按表1) 。
图3 自动超声检验用动态试样
5 检验仪器和设备
5.1 探伤仪
所用探伤仪的性能应符合GB /T 8651或JB / T10061的有关规定。
5.2 换能器
5.2.1 压电直探头的选用如表3。
不管选用哪种探头,都要保证有效探测区。板厚大于60mm时,若双晶片直探头性能指标能达到单晶片直探头,也可选用双晶片直探头。
表3的应用
板厚/mm |
所用探头 |
探头标称频率/MHz |
6-13 |
双晶片直探头 |
5 |
>13-60 |
双晶片直探头或单晶片直探头 |
≥2.0 |
>60 |
单晶片直探头 |
≥2.0 |
5.2.2 双晶片直探头的性能应符合附录A的要求。
5.2.3 当采用板波法进行探伤时,波型、波模及检验方法的选择应符合GB /T 8651的要求。
5.2.4 当采用横波探伤时,可参照JB 4730 – 1994的附录H。
6 检验条件和方法
6.1 原则上在钢板上加工完毕后进行,也可在轧制后进行。
6.2 检验面
可以从钢板任一轧制面进行检验,被检验钢板的表面应平整,应清除影响检验的氧化皮、腐蚀、油污等。
6.3 检验灵敏度
6.3.1 用压电探头时,检验灵敏度应计入对比试样与被检验钢板之间的表面耦合声能损失(dB)。
6.3.2 用双晶片直探头检验时,用图1试样或在同厚度钢板上将第一次底波高度调整到满刻度的50%,再提高灵敏度10 dB作为检验灵敏度。
6.3.3 用单晶片直探头检验时,灵敏度按图2试样平底孔的第一次反射波高等于满刻度的50%来校准。
6.3.4 板厚大于探头3倍近场区时,检验灵敏度用计算法、通过第一次底面回波高度来确定。
6.3.5 在动态状况下,也可利用4.4中所述的动态试样中相应的缺陷,在无杂波的情况下,使人工缺陷反射波高不低于仪器荧光屏刻度的50%,再提高10 dB作为检验灵敏度。
6.4 探头扫查形式
6.4.1 用压电探头时,探头沿垂直于钢板压延方向、间距不大于100 mm的平等线进行扫查;在钢板周围50 mm(板厚大于100 mm时,取板厚的一半)及坡口预定线(由供需双方在合同或技术协议中确定具体位置)两侧各25 mm内沿周边进行扫查。
6.4.2 用双晶片探头时,探头隔声层应与压延方向平行(垂直于压延方向扫查)。
6.4.3 根据合同或技术协议或图纸要求,也可进行其他形式的扫查或100%扫查。
6.4.4 自动检验也可沿平行于钢板压延方向扫查。
6.5 检验速度
检验速度应不影响探伤,但在使用不带自动报警功能的探伤装置进行扫查时,检验速度不大于200mm/s。
7 缺陷的测定与评定
7.1 在检验过程中,发现下列情况应记录
7.1.1 缺陷第一次反射波(F1)波高大于或等于满刻度的50%。
7.1.2 当底面第一次反射波(B1)波高未达到满刻度时,缺陷第一次反射波(F1)波高与底面第一次反射波(B1)波高之比大于或等于50%。
7.1.3 当底面(或板端部)第一次反射波(B1)波高低于满刻度的50%。
7.2 缺陷的边界或指示长度的测定方法
7.2.1 检验出缺陷后,在周围进行检验,以确定缺陷的延伸。
7.2.2 用双晶片探头确定缺陷的边界或指示长度时,探头移动方向应与探头的隔声层相垂直。
7.2.3 利用半波高度法确定缺陷的边界或指示长度。
7.2.4 确定7.1.2中缺陷的边界或指示长度时,移动探头,将板底面(或端部)第一次反射波升高到检验灵敏度条件下荧光屏满刻度的50%。此时,探头中心点即为缺陷的边界点。
7.2.5 采用自动超声波方法检验时,发现可疑缺陷后,缺陷的定量定位可用手工方法进行。缺陷的指示长度及边界的精确测定亦用人工方法。
7.3 缺陷指示长度的评定规则
单个缺陷按其表现的最大长度作为该缺陷的指示长度,若指示长度小于40 mm时,则其长度可不作记录。
7.4 单个缺陷指示面积的评定规则
7.4.1 单个缺陷按其表现的面积作为该缺陷的单个面积指示面积。
7.4.2 当多个缺陷的相邻间距小于100mm或间距小于相邻缺陷(以指示长度来比较)的指示长度(取其较大值)时,其各块缺陷面积之和也作为单个缺陷指示面积。
7.5 缺陷密集的评定规则
在任一1 m×1 m 检验面积内,按缺陷面积占的百分比来确定。
8 钢板的质量分级
8.1 钢板质量分级见表4。
8.2 在钢板周边50 mm(板厚大于100mm时,取板厚的一半)可检验区域内及坡口预定线两侧各25mm内,单个缺陷的指示长度不得大于或等于50mm。
表4 钢板质量分级
级别 |
不允许存在的单个缺陷的指示长度/mm |
不允许存在的单个缺陷的指示面积/cm² |
在任一1 m×1 m检验面积内不允许存在的缺陷面积百分比/% |
以下单个缺陷指示面积不记/ cm² |
I |
≥80 |
≥25 |
>3 |
<9 |
II |
≥100 |
≥50 |
>5 |
<15 |
III |
≥120 |
≥100 |
>10 |
<25 |
IV |
≥150 |
≥100 |
>10 |
<25 |
9 检验报告
检验报告应包括下列内容:
a) 工件情况:材料牌号、材料厚度等;
b) 检验条件:探伤仪型号、探头类型、探头标称频率、晶片尺寸、耦合剂、对比试样等;c) 检验结果:包括缺陷位置、缺陷分布示意图、缺陷等级及其他;
d) 检验人员、报告签发人的姓名及资格等极、检验日期、报告签发日期等。
附录A
(规范性附录)
双晶片直探头性能要求
A.1探头性能
A.1.1 距离—波幅特性曲线
用图所示试样测定每一厚度的回波高度,作出如图A.1所示的特性曲线,其必须满足下述条件:
A.1.1.1 要检测的最大厚度的底面回波高度与最大回波高度差应在0dB~-6dB的范围内。对于与具有距离幅度补偿功能的仪器联合使用的双晶片直探头,补尝后要求检测的最大厚度的底面回波高度与最大回波高度差也应在0dB~-6dB的范围内。
A.1.1.2 距离为3mm处的回波高度与最大回波高度差应在0dB~-6dB的范围内。对于与具有距离幅度补偿功能的仪器联合使用的双晶片直探头,补偿后要求距离为3mm处的回波高度与最大回波高度差也应在0dB~-6dB的范围内。
A.1.2 双晶片探头的表面泄露回波高度
直接接触法测得的双晶片探头的表面泄露回波高度必须比最大回波高度低40dB。
A.1.3 检出灵敏度(用图A.2试样测量)
图A.2试样平底孔的回波高度与最大回波高度差必须在-10dB±2dB的范围内。
A.1.4 有效波束宽度
使探头对准A.2试块ф5.6mm平底孔,并平等于双晶探头的声场分割面移动,测定最大回波高度两侧下降6 dB的范围,全部宽度必须大于15mm。

L0 —— 图1试样中最大回波高度时的厚度; L —— 使用的最大厚度。
图 A .1 距离—波幅特性曲线
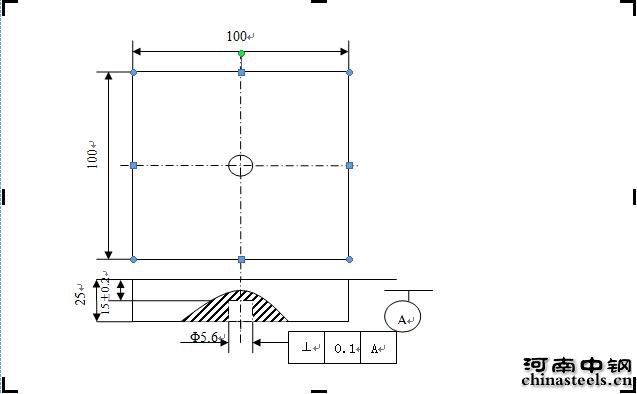
注:图中尺寸单位均为mm。
图 A.2 测定仪器和探头组合性能试样
厚度≥6mm扁平产品超声波检验方法(反射法)
EN10160:1999
1 范围
本欧洲标准描述了用超声波检验无涂层的扁平产品内部不连续(缺陷)的一个方法。它适用公称厚度范围为6mm-200mm的非合金或者合金钢扁平产品,不包括奥氏体钢或者奥氏体—铁素体钢。但是,只要噪声信号和回波探测临界值振幅之间的差值相对于规定极限足够大,则本标准可以适用于后面这种类型的钢材。
本标准按照第九款规定的准则,对扁平产品本体规定了四个质量等级(S0,S1,S2,S3),对边缘规定了五个质量等级(E0,E1,E2,E3,E4)。
对其他的检验方法或检验设备,如果在本标准的条件下可获得同样结果的话,厂家也可以采用。在有冲突的情况下,仅以本标准定义的方法为准。
厚度小于6mm扁平产品的检验必须经相关方特殊同意。
通常在生产地点进行检验,或根据供货方的许可。如果合同规定,检验可以在买方或其代表在场时进行。
2 参考标准
本标准使用了由其它出版社出版的注明日期或没有注明日期的参考标准。这些参考标准在本文适当的地方被引用并且列出了出版社的名称。对于注明日期的参考标准,本标准引用时仅使用其修补或修订本。没有注明日期的参考标准,仅使用其出版物的最新版本。
EN473,无损检验人员的资格和证明-总则
PrEN1330-4,无损检验-术语-第四部分;无损检验中使用的术语。
3 术语和定义
在PrEN1330-4中给出的定义和下列定义适用:
3.1内部不连续
在扁平产品厚度范围内的任何缺陷,如平面或层状缺陷、单面或多面夹杂带或群。
注:本文中指的是不连续。
3.2缺陷
不可接受的内部不连续,即超过规定的最大尺寸或分布密度极限。
3.3分布密度
在每一规定的本体面积或每一规定边缘区域的长度内,尺寸大于一个规定的最小尺寸和小于一个规定的最大尺寸的单个内部不连续点的数量。
3.4人工和辅助人工检验
有操作者使用一个或几个超声波探头置于扁平产品表面进行检验,并且在钢板表面进行适当的扫描,通过直接观察或通过固定的信号振幅显示装置,在显示屏上目示检查超声波信号。
3.5自动或半自动检测
采用机械的方法,使用一个或几个超声波探头,在扁平产品表面制作适当的扫描线,通过电子方式评定超声波指示信号。这样的检验可以无需操作者参与,是完全自动化的,或由操作者完成基本的设备操作功能,即半自动检验。
4 原理
采用的原理是超声波信号的反射(通常是纵向的),其平均方向垂直于产品表面。
检测包括:
(a) 通过比较缺陷回波的高度与缺陷同深度处给定直径的平底孔回波的高度来确定任一缺陷位置。
(b)然后确定缺陷区域,不连续区域由探头中心位置确定,对应考虑缺陷回波高度为最大高度一半的缺陷(6dB方法)。
对所有厚度扁平产品的探测在第一超声扫描中完成且仅从一侧执行。
5 人员
检验由符合EN473要求的具有3级资格证书的人员来完成。
6 设备
6.1说明
探测设备应该配有一个示波器屏幕,可以跟踪通过材料的超声波的路径。示波图应该是清晰可见的,连续回波的对应峰值应该是明显和非常清晰的;设备应适当校准过且装有分贝标记的放大器。
可以使用带显示器的超声检测设备和刻有dB的放大控制装置,或无显示器的设备。无显示器的设备应该能够完成自动振幅检测和评定,且其测量装置应该是按dB校准。
应该可以调节放大率,功率和扫描基线。
设备至少包括一个探头,它可以是一个单晶探头,既可以发射又可以接收(单探头),亦可是双晶探头(有独立的发射——接收转换器)。发射及接收的波的平均方向应垂直于产品的表面。
探头应有一定的频率及尺寸,以保证检验范围内要求的灵敏度。
单探头的盲区要求尽可能地小,也就是说:盲区应为扁平产品厚度的15%或15mm,取其较小者。双晶探头的焦点应适合扁平产品的厚度。
探头的主要尺寸为直径100mm至25mm,探头的公称频率为2MHz到5MHz之间。如果满足本标准的主要要求,较大尺寸和额定频率超出2MHz至5MHz范围之外的探头可用于自动或半自动检验和或当扁平产品呈现出高衰减时。
如表1所示,探头类型取决于产品的厚度。
表1——探头的类型
扁平产品的公称厚度(e)
或任一缺陷区的深度mm |
探头的类型 |
6≤e<60 |
双晶探头 |
6≤e≤200 |
单或双晶探头a)b) |
a) 如有冲突,所用的探头类型由协议规定。
b) 在用液浸法或水柱技术进行自动检验时,厚度小于60mm允许用单晶探头。 |
探头可以手持,亦可装在连续检测的设备之上,该设备的扫描速度足够低,以便于确定缺陷位置,并考虑到屏幕显示的滞后性,或者安装一个缺陷显示装置。
当使用双晶探头时,两个晶片的隔离层的方向,应垂直于扫描的方向。
设备的验证工作,应按有关的国家标准进行。
6.2设备是调节
设备投入使用前要对扫描基线、功率及放大率的特别要求进行确定。将扫描基线调整到一个值,此值使得示波器屏幕上,发射回波与底面回波之间的距离,足以清晰地显示出允许缺陷回波。
至少应显示两个底面回波。
功率与放大率的调节,应在无任何缺陷回波的完好区域上,同是4进行。第一次底面回波,可调至设备线性区域与屏幕高度相适应的最大波高(一般来说,在全屏幕高度的80%至100%之间)。
至少每隔8小时,应校正一次设备。
7 耦合条件——扁平产品的表面状态
耦合介质,应保证探头与扁平产品表面之间有充分的接触,通常用水作介质,但供方可决定用其他耦合介质(如:油、糊状物)。
表面状态,应允许当探头放在无内部缺陷的任何区域上时,可区分出至少两次连续的底面回波;扁平产品,通常不需作任何特殊的表面处理,便可进行检测。
8 扫描方法
8.1总则对扁平产品本体来说,检测是基于统计方法,除非订单中另有说明。按照质量等级,扁平产品的扫描按8.2或和8.3执行。在订货时经商定,可以提供特定区域或扁平产品本体的扫描,操作条件也应包含在协议中。
8.2扁平产品本体检验
8.2.1 S0及S1级的扁平产品
扫描包括,沿平行于扁平产品的边缘200mm见方格子线进行的连续检验,或沿表面上均匀分布的平行线(或振动线),给出相同的控制程度。
8.2.2 S2及S3级的扁平产品
扫描包括,沿平行于扁平产品的边缘100mm见方格子线进行的连续检验,或沿表面上均匀分布的平行线(或振动线),给出相同的控制程度。
8.3钢板边缘的检验
扫描包括表2对沿扁平产品四周边缘的区域的全部检测
表2扁平产品边缘区域的宽度
扁平产品的厚度e,mm |
区域宽度mm |
6≤e<50
50≤e<100
100≤e≤200 |
50
75
100 |
9 步骤
9.1灵敏度和设置范围
对每一种型号的探头,应给出使用的曲线:
a) 底面回波高度变化随扁平产品厚度变化的曲线;
b) 平底孔回波高度随其深度、孔直径变化的曲线;
——11mm孔适用于S0,S1,E0和E1级;
——8mm孔适用于S2,E2和E3级;
——5mm孔适用于S3和E4级;
孔的底部要尽可能平整,平行于超声波入射面并且无显著降低其超声波反射能力的凹坑或划痕标志。平底孔的直径和凹口宽度允许偏差为+5%。只要使用同样的设备/传感器类型组合,选定凹口的长度和宽度提供一个基本上等同与从规定平底孔得到的超声波信号反射,允许使用矩形槽。
当采用双晶探头检验时,对于所有质量等级,只用5mm直径孔,因为相应于8mm和11mm直径孔的特性曲线与底面回波曲线相互干扰、难以分清。
应采用试块确定这些曲线(分度试块测定底面回波高度变化的曲线;具有不同深度的平底孔的试块用于 测定直径为11mm、8mm和5mm的特性曲线)。试块由组织均匀的碳钢组成,每一条曲线至少应在探头使用范围内取5点确定。探头生产厂可提供所有这些曲线。
这样,对于给定厚度的扁平产品,此方法为:将底面回波高度调整到底面回波高度变化曲线上的某一值,并根据选定级别 ,将缺陷的回波高度与回波特性曲线(指11mm,8mm和5mm直径孔)相比较。仅当缺陷的回波高度大于特性曲线的高度时,才将记为缺陷。
9.2不连续( 缺陷)面积确定
9.2.1扁平产品本体检验
9.2.1.1用双晶探头检验
所有超出特性曲线的不连续( 缺陷)区应使用6dB法来确定,也就是不连续( 缺陷)范围由不连续( 缺陷)的反射高度等于底波最大高度一半时的探头中心位置确定。接着,确定包含整个不连续( 缺陷)的矩形,主要尺寸是不连续( 缺陷)的宽度。这样矩形的面积就可以计算出来了。
矩形的面积定义为不连续(缺陷)的面积S。如果两个相邻的不连续(缺陷)之间的距离小于或等于两者间较小的长度时,这两个不连续(缺陷)应考虑为一个不连续(缺陷),其面积为两个不连续(缺陷)面积的总和。
9.2.1.2单探头检验
检验包括:
a) S0和S1级的扁平产品:依照8.2.1中定义的方法确定面积。
b) S2和S3级的扁平产品:当使用5mm,8mm和11mm直径孔的特性曲线进行检测时,简单计算不连续(缺陷)个数。
确定方法如下:
——对于S2级:确定出回波的高度大于11mm直径特性曲线的不连续(缺陷)数量以及回波高度在8mm和11mm直径孔特性曲线之间的不连续(缺陷)数量N2(表4);
——对于S3级:确定出回波的高度大于8mm直径特性曲线的不连续(缺陷)数量以及回波高度在5mm和8mm直径孔特性曲线之间的不连续(缺陷)数量N3(表4)。
9.2.2边缘检验
检验包括与扁平产品本体(9.2.1)同样条件下,在8.3中所确定的不连续(缺陷)四周边缘(或按照简图焊接区域)的整个表面进行扫查。
确定方法如下:
——平行于扁平产品边缘方向的不连续(缺陷)最大尺寸L
max和最小尺寸L
min;
——不连续(缺陷)的面积(S);
——每1米长度内小于最小面积(L
max)、大于最小尺寸L
min的不连续(缺陷)数量。
用6dB方法确定不连续(缺陷)的性质。
10 验收标准
表3和表4按照探头使用类型,给出了扁平产品本体4个质量等级的验收标准(S0,S1,S2,S3),表5给出了5个边缘等级(E0,E1,E2,E3,E4)(参看图1)。
依照订货协议,可以供应与本体和/或四周边缘具有不同的质量等级的扁平产品。
11 检验报告
当要求时,生产厂应提交的检验报告应至少包括以下几点:
a) 参照的当前欧洲标准
b) 被检验扁平产品的参考数据(钢级,热处理状态,表面状态,尺寸);
c) 超声波探头(类型,尺寸,频率)和设备的特性;
d) 操作条件(耦合介质,扫描,采用的面积确定方法,设备的调节);
e) 检验结果;
f) 特殊协议中所提的特殊点;
g) 检验报告日期。
表3 用双晶探头检验厚度,<60mm的扁平产品本体的验收标准
等
级 |
不可接受的单个
不连续(缺陷)
mm² |
可接受的群集不连续(缺陷) |
|
考虑的面积a
mm² |
不允许超过的最大密度 |
S0
|
S﹥5000 |
1000<S≤5000 |
在最密集出的1m×1m见方的
区域内:20 |
S1 |
S﹥1000 |
100<S≤1000 |
在最密集出的1m×1m见方的
区域内:15 |
S2 |
S﹥100 |
5<S≤100 |
在最密集出的1m×1m见方的
区域内:10 |
S3 |
S﹥50 |
20<S≤50 |
在最密集出的1m×1m见方的
区域内:10 |
a) 上述群集(参看9.2)中每一个缺陷面积。
注意:对于缺陷尺寸,如果使用的方法是不用于6dB法的其它合适的方法,那么厚度≥60mm时此表亦可使用。
表4 用直探头检验扁平产品本体的验收标准
等级 |
不可接受的单个
不连续(缺陷) |
可接受的群集不连续(缺陷) |
考虑的尺寸a
(数值) |
不允许超过的最大数量 |
S0 |
S﹥5000 mm² |
1000<S≤5000mm² |
在最密集出的1m×1m见方的区域内:20 |
S1 |
S﹥1000 mm² |
100<S≤1000 |
在最密集出的1m×1m见方的区域内:15 |
S2 |
波高大于Φ11mm平底孔特性曲线的不连续(缺陷) |
N2
(Φ8mm-Φ11mm之间) |
在最密集出的1m×1m见方的区域内:10 |
S3 |
波高大于Φ8mm孔特性曲线的不连续(缺陷) |
N3
(Φ5mm-Φ8mm之间) |
在最密集出的1m×1m见方的区域内:10 |
a) 上述群集区每一个缺陷的尺寸(参看9.2)。
表5 检验扁平产品边缘的验收标准
|
允许的单个不连续
(缺陷)尺寸 |
考虑的最小不连续
(缺陷)尺寸 |
每一米长度内小于最大面积Smax且大于Lmin的不连续允许(缺陷)数 |
等
级 |
最大尺寸
Lmax
mm |
最大面积
Smax
mm² |
Lmin
mm |
E0 |
100 |
2000 |
50 |
6 |
E1 |
50 |
1000 |
25 |
5 |
E2 |
40 |
500 |
20 |
4 |
E3 |
30 |
100 |
15 |
3 |
E4 |
20 |
50 |
10 |
2 |
注:对于厚度≥60mm的产品,用11mm,8mm,5mm的平底孔特性曲线来计算缺陷数量。
——E3 缺陷回波高度在直径为8mm和11mm的平底孔特性曲线之间的缺陷数量:3
——E4 缺陷回波高度在直径为5mm和8mm的平底孔特性曲线之间的曲线数量:2
德国超声波检验厚钢板的技术交付条件
SEL072—77
1 适用范围:
这些交付条件适用于厚钢板,该厚钢板是采用超声波检验其内部缺陷的,例如分层和粗大夹杂。
2 概念:
根据这些交付条件进行的超声波检验适用于厚钢板,由制造厂在规定范围内(见第4节)进行的超声波检验(见第5节)能真正做到厚板中无缺陷。为此,将超声波检验分为超声波平面检验、边缘检验和全面检验。
3 分类:
3.1 根据此供货条件进行超声波检验的厚钢板的分类标准见表1和表2,并与检验方法无关,表1的分类适用于平面检验。表2的分类适用于边缘检验。
3.2 根据表1或表2选择等级是用户所关心的。所以,在要考虑的说明或技术规程内的规定应该遵守(对此可看4.2.1和4.3.1节),在订货时必须规定,这些交付条件必须遵守附带的有关钢种的质量规范,同时必须确定厚板空间应该提供哪一类检验;
根据表1中的等级之一的超声波平面检验(见4.2)节;
或者根据表2中等级之一的超声波边缘检验(见4.3节);
或者根据表1和表2中等级之一的超声波全面检验(见4.4节)。
如果在订货时并未明确规定采用那一类等级的话,一般可采用3级作为协定的等级。
4 要求:
4.1遵照表3的规定,厚板超声波检验的要求必须指明厚板空间是作超声波平面检验、超声波边缘检验还是全面检验(见3.2节)。
4.1.1平面检验是在钢板表面进行检验。不需特别考虑边缘区域。
4.1.2边缘检验仅检验各边缘。
4.1.3全面检验包括在钢板上表面的检验和边缘的检验。
4.2对于进行超声波平面检验的厚板必须按协定的等级满足表1中规定的要求。
4.2.1对供方来说,表1中的每一类交付条件都可达成协议。在一般情况下,特别的适合于应用的交付条件是不必要的。但必须规定,按交付条件进行超声波平面检验的厚钢板应满足表1中的3级标准。
4.3对于进行超声波边缘检验的厚板必须按协定的等级满足表2规定的要求。
4.3.1对供方来说可按表2中的每一类交付条件达成协议。在一般情况下,特别的适合于应用的交付条件是不必要的。但必须规定,按交付条件进行超声波边缘检验的厚钢板应满足表2中的3级标准。
4.4对于进行全面超声波检验的厚板。必须按协定的等级满足在表1和表2中相同等级规定的要求,对于按表1中5级和6级标准进行全面超声波检验的厚板而言,在作边缘检验时必须履行表2中的4级标准。
4.4.1对供方来说可按表1和相应的表2中的每一类交付条件达成协议,在一般情况下,特别的适合于应用的交付条件是不必要的。但必须规定,进行全面超声波检验的厚钢板必须按本供货条件满足表1和表2中的3级标准。
4.5对平面和边缘有不同要求时,等级必须分别按4.2节和4.3节达成协议。
5、检验:
5.1每一块厚板(或板坯)的检验由于某种原因制造厂在一个合适的区域内进行。为此,超声波检验方法和检验条件的选择均由制造厂决定。制造厂还必须决定在哪一种热处理条件下检验,到目前为止在技术规程上(如AD说明书)尚未采取另外的规定。
注:①应该准备有关厚钢板超声波手工检验的欧洲标准。
在订货时,必须就检验区域达成协议,同时,要求的等级必须通过计算选定,在一般情况下,平面检验可按边长为20cm的格子或按一个笔直的相互平行间距为10cm的梳状检验线进行,或按一组正弦状检验线进行检验,这些正弦曲线的的振幅和振荡半周长均为20cm,在作边缘检验时,距切口的宽度等于被检钢板的厚度,但至少为2.5cm。
5.2订货时,必须就在制造厂检验时用户或他的代理人是否到场达成协议,同时必须就保证生产过程中不受妨碍的检验措施达成协议。
5.3在有争议的情况下,可以按补充说明里的有关规定进行检验,当制造厂和用户或他们代理人之间就评价已经确认的缺陷尺寸和或个数上存在分歧时,只能根据本供货条件的内容给以仲裁。
6 索赔:
6.1只有当缺陷超过了订货时规定等级所允许的尺寸和/或个数,并且钢板的适用性受到某些损害时,可就缺陷要求索赔。
6.2用户应给制造厂以机会,通过索赔样品和供给钢板例证所提供的索赔理由,让制造厂自己承认索赔数。
表1 根据交付条件进行厚钢板超声波平面检验的等级分类
等级 |
最小的必须考虑的
缺陷面积cm |
最大的允许缺陷
面积cm |
缺陷的允许个数① |
指钢板的局部区域②
每m |
指整张钢板每
m |
0 |
0.5 |
取消 |
0 |
0 |
1 |
0.5 |
1 |
≤4 |
≤2 |
2 |
0.5 |
1 |
≤30 |
≤15 |
3 |
1 |
10 |
≤10 |
≤5 |
4 |
1 |
10 |
≤50 |
≤30 |
5 |
10 |
100 |
≤1 |
≤1每2m |
6 |
10 |
100 |
≤5 |
≤3每2m |
注:①当面积为1cm²至10 cm²(参看1级至4级)的相互靠近的缺陷的边缘距离小于的缺陷的最大延伸长度时,这些缺陷必须看作一个缺陷,但这只适用于两个缺陷的评价。当两个以上的缺陷紧靠在一起时,每次必须逐对进行比较;②每平方米的数据是指1米×1米和面积;③0级只适用于特别协议。例如某些特定表面区域。
表2 按照交付条件进行厚钢板超声波边缘检验的等级分类
等级 |
最小的必须考虑
的缺陷的面积cm² |
最大的允许
缺陷面积cm² |
必须考虑的平行于
切口的缺陷的最大
允许长度cm |
缺陷的允许个数①
每m² |
0② |
0.5 |
取消 |
取消 |
0 |
1 |
0.5 |
1 |
4 |
≤2 |
2 |
0.5 |
1 |
4 |
≤5 |
3 |
1 |
10 |
4 |
≤3 |
4 |
1 |
10 |
4 |
≤5 |
注:①当面积为1cm²至10 cm²(参看1级至4级)的相互靠近的缺陷的边缘距离小于缺陷的最大延伸长度时,这些缺陷必须看作一个缺陷,但这只适用于两个缺陷的评价。当两个以上的缺陷紧靠在一起时,每次必须逐对进行比较;②
0级只适用于特别协议。例如某些特定边缘区域。
表3 对厚钢板的超声波平面检验,边缘检验和全面检验要求的等级
检验的种类 |
要求检验 |
必须满足的要求 |
按其一等级进行超声波检验 |
在一般情况下超声波检验的等级 |
超声波平面
检验 |
平面 |
按表1中某一等级 |
按表1中3级 |
超声波边缘
检验 |
边缘 |
按表2中某一等级 |
按表2中3级 |
超声波全面
检验 |
平面
边缘 |
按表1中某一等级
和按表2中相同等级① |
按表1中3级
按表2中3级 |
注:①如果采用表1中的5级和6级,钢板边缘检验必须满足表2中的4级供货条件。
超声波检验厚钢板的技术交付条件
----在超声波检验发生争议时执行
(钢铁交付条件072-77的附件)
1 适用范围:
在有争议的情况下,本章适用于根据钢铁交付条件072进行的厚钢板超声波手工检验。即在某种情况下,一旦制造厂和用户或他们的代理人之间,在评价已查明的缺陷面积和个数上产生了分歧,在这种情况下,必须规定检验过程的各项细节,通过这样的检验,可以被查明有争议的缺陷面积和个数。
2 检验方法:
2.1在任何情况下可以使用脉冲反射法。
为了测定缺陷的面积,应该尽可能应用半波高度测定法。在这里,置于缺陷上的探头在各个不同的方向往复移动,以便确定缺陷边缘位置,在这些位置上中间回波的高度等于当时最高值的一半,边缘各点的连接线形成了要测定缺陷表面的界线(详情见5.1节)。
当小缺陷处于较大深度时,这种方法会不精确,在这种情况下,必须按照距离-增益-面积(AVG)曲线图确定缺陷的当量面积(详情见5.2节)。
2.2因此,可以根据检验任务应用下面的检验方法:
A 按照中间回波的半高测定方法确定缺陷面积;
B 采用适合使用探头的距离-增益-面积(AVG)曲线网来确定缺陷的当量面积。
3 对受检钢板上表面的要求
受检钢板的上表面必须处于这样的状态以便保证进行的检验是无可非议的,在一般情况下,交货状态下的轧制钢板的光滑上表面是足够的。
4 对检验设备的要求
4.1检验调整
检验时必须调整到这样的状态,保证探头垂直接通;探头的运行可以选择手动的方式或机械传动的方式。
4.2探伤仪
可以使用下面的超声波探伤仪:
4.2.1仪器具有萤光屏显示图和用分贝(dB)刻度的增益调节器。
具有萤光显示图和用分贝(dB)刻度的增益调节器的探伤仪的灵敏度必须这样调整:使要评价的反射波的高度保持在萤光屏幕图可利用高度的20%-80%之间。
4.2.2不带萤光屏显示图的检验系统能自动进行脉冲高度的测量和评价,在这种情况下,测量单位必须用分贝(dB)调整。
4.3探头
选择探头按表1进行。
4.3.1当采用检验方法A时(见2.2节),仅能使用带有分割式发射和接收振荡器的探头(SE)。
4.3.2当小缺陷处于较深距离并采用标准探头(即直探头)时,可应用检验方法B(见2.2节)。
5 检验的进行
首先是测定缺陷的位置并确定探头对缺陷的距离(5mm当量缺陷面积的评价界线)。
为了测量已检出的缺陷面积,要依赖与表1中相应的缺陷距离来选择探头和方法。
5.1当使用检验方法A时(见2.2节),探头移动到有疑问的部位上,并确定半值宽,这时可确定对应的两点,在这两点上中间回波的高度为完好部位高度的0.5倍(即6 dB半益差)。这两点的确定决定了探头的中心,这两点被认为是缺陷相对的两个边缘点。每次将探头移到另外的方向上,按相应的方式可得到缺陷其它的边缘点。借助于波束截面的面积及其形状,能确定要测定的缺陷面积的最小值,在用SE探头时,轮廓是椭圆形的,并随距离面发生变化,密切协作 里,就距离范围而言。最有利的扫描方向由表1中注1规定。
5.2当采用B法时(见2.2节),可调节增益的分贝(dB)来测定有疑问的部位。必须将涉及的缺陷的第一次反射波调整到完好部位珠(即稳定)第一次底波的高度,借助于增益值的变化量△V。
B,可以从距离-增益-面积(AVG)曲线图(图1)查出当量缺陷的直径(一种完整的反射体,例如平底孔反射体),这个当量缺陷的直径如同有疑问的缺陷。为此,如图1所示的例子,将底波曲线上厚度为板厚(例如140mm)的X点向下移动一个增益值△V(例如14 dB)。这样可延长到y点作一条平行于横坐标的直线,这条直线与通过等于缺陷距离深度(例如为75mm)的平行于纵座标的直线在E点处垂直对穿,在曲线族中与图中E点离得最近的那条曲线已补绘了人工当量缺陷面积(例如直径为5mm)。当量面积和真实缺陷面积相等。图1描述的AVG曲线图仅适用于频率为2MHZ有效振荡器(晶片)、直径为24 mm的标准探头(即直探头)。
表1 缺陷距离、探头和检验方法之间的关系
缺陷距离(mm) |
探头型号① |
检验方法② |
≤20 |
SE5º |
A |
20-60 |
SE0º |
A |
>60③ |
N缺陷当量直径≤11 mm,B |
SE0缺陷当量直径>11 mm,A |
注:①SE5=SE探头(即TR探头),频率为4MHZ,双斜角度约为5 º,焦距约为12 mm,振荡器直径为9-20 mm。当振荡器直径≤10 mm时,则探头探查方向垂直于隔声层;SE0=SE探头,频率为4MHZ,双斜角度约为0º,焦距约为25-40 mm,振荡器直径为18-20 mm。探查方向平行于隔声层。N=直探头(即标准探头),频率为2MHZ,振荡器直径为24mm.②见2节。③当缺陷距离上表面的距离超过60 mm时,首先必须采用检验方法B,当按这个方法(B)探查的缺陷面积超过直径为11 mm的当量缺陷时,必须采用检验方法A并使用SE0探头。
钢板超声直射波检验的标准规范
ASTM A435/A435M-90
1
适用范围
1.1 本规范包括厚度大于或等于1/2英寸(12.5mm)轧制全镇静碳钢和合金钢板进行直射声束,脉冲回波法的超声检测规程和验收标准。制定本标准是为了保证交付的钢板示带有严重的内部不连续性,诸如缩孔、断裂或分层。每当征询、合同、订货单或规范指明要对板材进行超声检测时,均应使用本标准。
1.2 按照本规范规定进行检测的人员应具备ASNT SNT-TC-1A最新版本或被接受的对等标准规定的资格和证书。对等标准即为包括超声波无损检测人员资格和认证方面内容并为需方接受的标准。
1.3 无论用英制单位还是用国际单位制表示的数值,均可单独作为标准值。正文括号中的值为国际单位制值。用两种不同单位制表示的值并不完全等值,因此,只能采用其中一种单位制的值,两种单位制并用会产生不符合本规范的结果。
2
参考文件
2.1 标准:SNT-TC-1A
3
仪器
3.1 制造厂应为检测配置适当的超声仪器和必要的有资格的操作人员。所配设备应是脉冲回波直射声束型仪器。换能器一般是直径为1-1 英寸(25-30mm)圆晶片,或边长1英寸(25mm)的方晶片。当然,可以使用有效面积至少为0.7平方英寸(450mm²)的任何换能器。检测应用下列其中一个方法;直接接触法、浸入法或液体耦合法。
3.2 在评估和精确测定缺陷显示时允许使用其它探头。
4
检测条件
4.1 检测应在不影响设备正常工作的场所进行。
4.2 使板表面清洁平滑到扫查时足以使背面回波至少保持满刻度高度的50%。
4.3 由本方法检测的钢板,表面应去除残留的机油或铁锈。为了达到适当平滑度而磨掉的任何规定的标记在检测后应予以恢复。
5
检测方法
5.1 超声检测应在板的任一主平面上进行。近表面的验收缺陷可要求从另一平面检测,订购的淬火加回火板应在热处理后进行检测。

5.2 推荐的额定检测频率为2 MHz,因材料的厚度、晶粒度、或金相组织以及采用的仪器或方法变更可能要求更高或更低的检测频率。但只有同用户达成一致意见,才允许使用低于1MHz的频率。在检测时,应能得到一个清晰,易于解释的示迹波形。
5.3 检测时,仪器工作在一个检测频率上,使仪器调整到能在板的一个完好区获得的背面参考回波为(最小值)50%到(最大值)75%满刻度高,校准仪器时,将探头沿板表面扫查,扫查距离至少1T或6英寸(150mm),两者中选较大的一个值,记下背面回波位置。若检验时的背面回波位置同校准的有变化,应重新校准仪器。
5.4 应连续沿着相互垂直的格子线中心扫查,格子线间距为9英寸(225mm)或根据制造厂的选择,应连续地沿垂直于板的主压延方向的平行线进行扫查,扫查线间距为4英寸(100mm),或应连续沿平行于板主压延方向的平等线进行扫查,扫查间距为3英寸(75mm)或更小。应使用适当的耦合剂,如水、乳化油、甘油等。
5.5 扫查线应从板的中心或一个角上测量起,对板边沿宽度为2英寸(50mm)的带状区应作附加扫查。
5.6 采用沿格子线扫查的方式,在沿某一格子线扫查时,若出现背面回波完全消失并伴随有连续的不连续信号显示时,与有不连续信号显示处相邻方格的全部区域均应被连续扫查。采用沿平行线扫查的方式,若出现背面回波完全消失,并伴随有连续的不连续信号显示时,则以该处为中心的整个9×9英寸(225×225mm)方形区域均应连续扫查。存在这种状态区域的实际边界无论采用何种方式扫查,均应由下述技术予以确定,即将探头移离不连续的中心处,直到背面回波与不连续回波等高时,在该处标上标记重复上述操作直到确定整个边界。
6 验收标准
6.1 任何引起背面反射完全消失的不连续信号区域,只要它不能被一个直径为3英寸(75mm)或半板厚(取其大者)的圆包容,则按拒收处理。
6.2 制造厂有权就超声检测后对拒收的板在超声显示的缺陷进行修补问题上同用户进行讨论。
6.3 用户可派代表赴现场检测。
7 标记
7.1 应对符合本规范要求而予以验收的板材采用钢印或模板印刷方式,在材料规范要求的标记附近标上“UT435” 字样。
补充要求
订货单上另有规定时才可应用下列要求:
S1、在用户与制造厂达成一致意见时,以本条款来代替5.4和5.5条规定的扫查方法。应对板的一个主平面进行100%的扫查。扫查应沿平行或横越钢板轧制方向的平行线进行,每次扫查之间要有不低于10%的复查。
特殊用途的普通钢板与复合钢板超声直射波检验的标准规程
ASTM A578/578M---96

1 适用范围
1.1 本规程包括用脉冲反射式超声直射波检验的检验规程和验收标准,适用于特殊用途的厚度等于或大于3/8in(10mm)轧制的普通碳钢和合金钢钢板以及复合钢板。本方法用于探测与轧制表面平行的内部缺陷。提供了三种等级的验收标准。还为复合钢板的检验以及其它可用的检验规程提供了补充要求。
1.2 以英寸一磅单位或国际单位(SI)表示的值都应分别视为标准值。正文中SI单位在括号内示出。由于两种单位制的数字并非精确相等,故必须独立地分别采用。如果加以混用将导致标准的不一致。
2 引用标准
2.1 ASTM 标准
A263 耐腐蚀铬钢复合板、薄板和带材的材料技术标准;
A264 不锈铬—镍钢复合板、薄板和带材的材料技术标准;
A265 镍和镍基合金复合钢板的材料技术标准。
2.2 美国国家标准
B46.1 表面组织
2.3 美国国家标准
SNT—TC—A
3 订货需知
3.1 询价单和订货单应指明下列各项要求;
3.1.1 验收等级要求(第7和8条)除采购方与制造厂另有协议以外,应采用1级验收标准。
3.1.2 第5.2和2.1条以及第13条中所述对本规程的条款的任何补充要求。
3.1.3 补充要求(如有必要)。
4 仪器
4.1 校核波幅线性时,应将换能器置于IIW试块或相似试块的尝试分辨力测试槽的上方,使该项柄的反射信号近似为满波幅的30%,底面之一的反射信号近似为满波幅的60%(即为槽反射信号高度的两倍)。然后绘出一条指出偏离上面已建立的2:1比率的曲线,这种偏离出现在槽反射信号的波幅,按每次一格的刻度分格递增直到底面反射信号达到满波幅,然后再按每次一格的刻度递减,直到槽反射信号波辐降到一格刻度。测出每次变动的两个信号波幅之比值。对应较大一个信号的位置在图上绘出这些比值。在满波幅的20%至80%之间的范围内昆值的偏离应在2:1的10%以内,在检查进所用仪器的调整应不致引起超出上述已建立的10%的范围。
4.2 换能器应为1或11/8in.(25或30mm)的直径或lin.(35mm)见方。
4.3 也可采用其它的探头来评定和精确测定显示的信号。
5 检验规程
5.1 检查应在不干扰检测正常操作的场所进行。
5.2 除非另有规定,可在钢板的任一一个主要表面上进行超声波检验。
5.3 钢板表面应足够清洁和平滑,以使钢板底面的第一次扫查时至少能保持在满波幅的50%。可以按照制造厂的方案采用合适的方法去除锈皮。可以局部打磨比较粗糙的表面。为了达到适当的表面粗糙度而去掉的任何规定的识别标记,都应重新标上。
5.4 采用下述的方法之一进行检测:直接接触法,液浸法或液柱耦合法。采用合适的耦合剂,如水,可溶性油或甘油。用本方法测试的后果是钢板的表面允许残留有油或锈,或两者都有。
5.5 推荐采用21/4MHz的标称检测频率。当被检测的钢板厚度小于3/4.in(20mm)时,可能需要采用5MHz的频率。由于材料厚度,晶粒大小、显微组织以及仪器或方法的特性等原因,也可以要求改用较高或较低的检测频率。换能器应在其额定频率下使用,检验时,应能产生清晰而又易于辨认的扫描图像。
5.6 扫查
5.6.1 应沿标称中心距为9in. (225mm)的垂直格子线进行连续扫查,或是按照制造厂的方案,沿垂直于钢板主轴线的标称中心距为4in. (100mm)的平行线连续扫查。扫描线应从钢板的中心或某一个顶角开始量起,并在钢板的探测面上离所有的边缘不到2in. (50mm)处补加一条扫查线。
5.6.2 进行一般扫查时,调节仪器使其能从钢板无缺陷区的底面产生相当于50%到90%满波幅的第一次反射信号。监控器灵敏度的调整可与表面粗糙度相适应。
5.6.3 如果在一般扫查中发现有缺陷时,则调节仪器使其能从钢板无缺陷区域的底面产生相当于75±5%满波幅的第一次反射信号。在评定缺陷的状况时,应保持这一仪器调整值。
6 记录
6.1 记录所有能引起底面反射信号完全消失的缺陷。
6.2 对于厚度等于或大于3/4in. (20mm)的钢板,记录所有其波幅等于或大于50%初始底面反射信号,并伴随有50%底面反射信号损失的缺陷信号。
注:在始脉冲和第一次底面反射信号的中间出现的信号,其第二次反射信号可能会位于底面第一次反射信号之处。当出现这种情况时,应采用多次底面反射法作补充探测。
6.3 当沿格子线的扫查发现某一格子线上有6.1和6.2所述应记录的情况,则应对以这一信号处为中心的9×9in. (225×225mm)方格的整个表面区域作扫查,应采用下述技术方法之一测定这些应记录情况的真实边界:移动换能器离开缺陷的中心,直至底面反射信号与缺陷信号的高度相等。在钢板上标出相当于换能器中心的点。重复这种操作以测定其边界。
7 验收标准— A级
7.1 任何有一个或多个缺陷引起底面反射连续全部消失并伴随有在同一平面上连续缺陷信号的区域不能被一个直径为3in. (75mm)或1/2板厚的圆所包围(取大者)的均不能验收。
8 验收标准— B级
8.1 任何一个区域内有一个或多个使底面反射连续消失并伴随有在同一平面上连续缺陷信号的区域不能被直径为3in. (75mm)或1/2板厚的圆所包围(取大者)的均不能验收。
8.2 此外,小于8.1的规定,但有两个或更多个的缺陷时,也应拒收,除非其分隔的最小距离等于较大缺陷的最大直径,或者它们能被8.1所述的圆包围。
9 验收标准— C级
9.1 任何一个区域内有一个或多个使底面反射连续消失并伴随有在同一平面上连续缺陷信号的区域不能被一个1in. (25mm) 直径圆所包围的应拒收。
10 重新审议
10.1 制造厂保留有与采购方商讨经超声波检测被认为不合格的钢板的权利,目的是在拒收之前,能对这些由超声波检测指出有缺陷的部位作可能的修补。
11 检查
11.1 采购方的代表,在执行采购方的合同的整个过程中,可以随时到制造厂中对所订购的材料进行超声波检测,有关的各个部门作现场监督。制造厂应提供一切可能方便,以使代表满意地认为材料确是按照本规程供货的。除了另有规定以个,所有的检测和验证在进行时都不能妨碍制造厂的操作工序。
12 标记
12.1 按本规程验收的钢板,都应在其一个角上作漏字板印刷(或打标记):“UT — A 578—A”(对于A级)和“UT A 578—B” (对于B级)。“UT — A 578—C”(对于C级)。对订货的每一补充要求,应另加补充编号。
13 检验报告
13.1 除了采购方和制造厂另有协议以外,制造厂应报告如下数据:
13.1.1 将第6条所列出的所有应记录的信号,标在一张钢板草图上,在其上应有钢板几何形状的足够数据,并且草图与钢板的数据要安全相同。
13.1.2 所采用的测试参数,包括仪器制造厂和型号,检测频率,表面状况,换能器件类型和频率)以及耦合剂;
13.1.3 检验日期。
补充要求
这些补充要求仅适用于采购方单独规定时。当这些要求的细节本文未述及时,则应由制造厂和采购方双方协商确定。
S1 扫查
S1.1 对钢板表面进行100%连续扫查。
S2 验收标准
S2.1 第6条所列出任何应记录的情况若为:
⑴ 连续的;
⑵ 在同一平面上(板厚的5%以内);
⑶ 不能被一个3in. (75mm)直径的圆所包围。
两个或更多个的应记录的情况(见第5条),若:
⑴ 在同一平面多上(板厚的5%以内);
⑵ 各自能被3in. (75mm)直径的圆所包围;
⑶ 相互分隔的距离小于较小缺陷的最大尺寸;
⑷ 不能集中包围在3in. (75mm)直径的圆内。
也是不能验收的。
S2.2 比第7或8条有更多限制的验收等级应由制造厂与采购方协商采用。
S3 检验规程
S3.1 制造厂应按本规程提供书面的检验规程。
S4 资格证书
S4.1 制造厂应提供有关超声波检测人员资格评定的证书.
S5 表面粗糙度
S5.1 在测试前应将钢板的表面粗糙度处理到最大不超过25µin.(3µm)AA(参见美国车家标准ANSI B46.1)。
S6 整体结合复合钢板的检验 验收等级S6
S6.1 采用符合本规程的检验规程和技术,从复合层表面对钢板作检验。
S6.2按照I级标准,或当采购方有特殊地西游记时则按II级标准检查基体钢板。
S6.3 如果底面反射完全消失并伴随出现复合层与基体钢板界面的反射信号,则该复合层应判为未结合。
S6.4 除非另有规定,按S6.3确定的未结合显示如不能为3in. (75mm)直径的圆所包围,则应按适当的材料技术标准对复合层内缺陷修补的要求和范围进行补焊。
S6.5 本补充要求适用于下述标准:ASTM A263、A264、A265。
S7 整体结合复合钢板的检验 验收等级S7
S7.1 采用符合本规程的检验规程和技术,从复合层表面对钢板作检验,但规定作100%表面探测的除外。
S7.2 按照I级标准,或当采购方有特殊要求时,则按II级标准检查基体钢板。
S7.3 若复合层与基体钢板的交界面上有回波显示而同时钢板的底面反射信号完全消失,则该复合层应判为未结合。
S7.4 除非另有规定,按S7.3确定的未结合显示若不能被直径1in. (25mm)的圆所包围,则应按适当的材料技术标准对复合层内缺陷修补的要求和范围进行补焊。此外,如果补焊面积超过复合面的1.5%时,应预先得到批准。
S7.5 本补充要求适用于下述标准:ASTM A263、A264、A265。
S8 超声波检验,用平底孔校准(用于等于或大于4in. [100mm]的钢材)
S8.1 用下述校准和记录规程代替5.6.2、5.6.3及第6条。
S8.2 换能器应符合4.2条。
S8.3 参考反射体 应采用深度为T/4,T/2和3T/4的平底孔来校准仪器。平底孔的直径应按照表S8.1。各孔可以钻的被检钢板中,如果它们的位置不干扰钢板以后的使用,或钟点 在被检钢板的延长部分;或者钻在一块与被检钢板相同公称成分或热处理的参考试块中。参考试块的表面用肉眼观察应不优于被检钢板的表面。参考试块的厚度应与被检钢板的公称厚度相同[在被检钢板的75-125%或1in. (25mm)的范围内,取其小者],并且其声学特征应与被检钢板相似。声学相似性是指在不改变仪器调节的情况下,参考试块和被检钢板的底面反射信号的差别≤25%。)
表S8.1 不同钢板厚度的校准孔直径(S8)
钢板厚度
in. (mm) |
>1-4
(25-100) |
>4-8
(>100-200) |
>8-12
(>200-300) |
>12-16
(>300-400) |
孔径,in. (mm) |
1/8(3) |
1/4(6) |
3/8(10) |
1/2(13) |
S8.4 校准规程
S8.4.1 将探头耦合并置于能得出T/4,T/2和3T/4处各反射体最大波幅之处。调节仪器使给出最高波幅反射体的信号波幅达到满波幅的75±5%。
S8.4.2 不改变仪器的调节。将探头耦合并置于保孔的正上方,在示波屏上标出每个孔的最大信号波幅位置及每个最小 剩余底面反射高度。
S8.4.3 在示波屏上标出每个孔信号从扫描线至最大波幅标记处一半的垂直距离。将各孔的最大波幅标记点联成线,并延长此线使其包括整个厚度,此线即为100%DAC(距离波幅校正曲线)。同样,将各最大波幅一半的标记联成线并延长之,作为50%DAC。
S8.5 记录
S8.5.1 凡是剩余底面反射波幅小于S8.4.2所得最小剩余底面反射的最高波幅的所有区域均应记录。
S8.5.2 凡是信号超过50%DAC的所有区域均应记录。
S8.5.3 当沿给定的格子线探测出S8.5.1和S8.5.2中所列的应记录情况时,应继续扫查与该情况相邻方格的整个表面区域,并记录每一应记录情况的边界或范围。
S8.6 扫查应按照5.6。
S8.7 应按照采购方规定采用第7或第8条的验收等级,但应记录情况应按S8.5。
S9 电渣重溶(ESR)和真空电弧重熔(VAR)钢板的超声波检验,厚度从1-16 in. (25-400mm),采用平底孔校准和距离波幅校正
S9.1 被检验材料的表面粗糙度,对于≤8 in. (200mm)厚的板材最大为200µin.(5µm);对于>8-16 in. (25-400mm)厚的板材最大为250µin.(6µm)。
S9.2 采用下述规程代替5.6.1、5.6.2、5.6.3和第6条。
S9.3 换能器应符合4.2条。
S9.4 参考反射体 应采用深度为T/4,T/2和3T/4和平底孔来校准仪器。平底孔的直径应按照表S9.1。孔的平底孔与检测表面的平等度应在1°以内。各孔可以钻在被检的钢板中,如果它们的位置不一干扰钢板以后的使用;或者钻在被检钢板的延长部分;或者钻在一块与被检钢板公称成分和热处理的参考试块中。参考试块的厚度应与被检钢板的公称厚度相同[在被检钢板的75-125%或1in. (25mm)的范围内,取其小者],并且其声学特征应与被检钢板相似。声学相似性是指在不改变仪器调节的情况下,参考试块和被检钢板的底面反射信号的差别≤25%。
S9.1 不同钢厚度的校准孔直径(S9)
钢板厚度
in. (mm) |
>4-6
(100-150) |
>6-9
(>150-225) |
>9-12
(>225-300) |
>12-20
(>300-500) |
孔径,in. (mm) |
5/8(16) |
3/4(19) |
7/8(22) |
11/8(29) |
S9.5 校准规程
S9.5.1 将探头耦合并置于能得出T/4,T/2和3T/4处各反射体最大信号波幅之处,调节仪器使给出最高波幅反射体的信号波幅达到满波幅的75±5%.
S9.5.2 不改变仪器的调节,将探头耦合并置于各孔的正上方,在示波屏上标出每个孔的最大信号波幅。
S9.5.3 在示波屏上标出每个孔信号从扫描线至最大波幅标记处一半的垂直距离。将各孔的最大波幅标记点联成线,并延长此线使其包括整个厚度,此线即为100%DAC(距离波幅度校正曲线)。同样,将各最大波幅一半的标记联点成线并延长之,作为50%DAC。
S9.6 扫查 应该对钢板的一个主要表面进行100%扫查。探头各次扫查轨迹的间隔应能使毗邻的扫查至少有15%的重迭,以保证有足够的覆盖度来发现缺陷。
S9.7 记录 记录底面反射低于50%DAC的所有区域。如果底面反射的降低在示波屏上并不伴随有其他信号,应将该处的表面重新修整并重新作超声波检测。若底面反射仍然低于50%DAC,它的损耗就可能由被检材料的冶金结构所引起,此材料应搁置起来汴采购方和制造厂进行冶金方面的复查。
S9.8 验收标准 任何超过100%DAC的信号应被认为是不能验收的。制造厂可以保留与采购方讨论被超声波检验拒收的材料的权利,其目的是在板材判废之前,对超声波检测指子网掩码缺陷进行可能的修补。
A578 / A578M - 96与A578 /A578 M - 92的级别等同对照如下:
A578 / A578 M - 96 A578 / A578 M - 92
A级 II级
B级 I级
C级 III级
GJB
中 华 人 民 共 和 国 国 家 军 用 标 准
FL GJB
潜 艇 耐 压 壳 体 用 钢 板
超 声 波 探 伤 方 法
Ultrasomec examination on steel plate
for submarine qressure shell
国防科学技术工业委员会 批准
中 华 人 民 共 和 国 国 家 军 用 标 准
潜 艇 耐 压 壳 体 用 钢 板
超 声 波 探 伤 方 法 GJB
Ultrasomec examination on steel plate
for submarine qressure shell
1

范围
1.1 主题内容
本标准规定了潜艇耐压壳体用钢板超声波探伤方法及评定标准。
1.2 适用范围
本标准适用于潜艇用耐压壳体用厚度为6-80mm的10和钢板超声波探伤方法及评定。
本标准也适用于其它舰用钢板的超声波探伤。
2 引用文件
GB 11259 超声波检验用钢制对比试块的制作与校验方法
GJB 593.1 无损检测质量控制规范超声波纵波和横波械检验
ZB Y230 A型脉冲返射式超声波探伤仪通用技术条件
ZB Y230 超声波探伤用探头性能测试方法
JB3111 无损检测名词术语
3 定义 本标准所用术语定义见JB3111。
4 一般要求
4.1 钢板探伤采用直探头脉冲反射法。
4.2 探伤方式采用液浸法(包括局部水液法)或直接接触法。
4.3 超声波探伤原则上应在钢板制造厂钢板加工完毕后进行也可在轧制后进行。
4.4 耦合剂为水、机油、工业甘油等,其质量应符合GJB593第和条的规定。
4.5 探伤面为钢板任一轧制面。当有影响声耦合的氧化皮、锈蚀、油污等附着物时,必须清除。
4.6 从事钢板超声波探伤人员应经过培训并持有权威机关颁发的技术资格证书,签发探伤报告人员必须持有II级或II级以上超声波探伤资格证书。
5 详细要求
5.1 探伤装置
5.1.1 超声波探伤仪
5.1.1.1采用A型脉冲反射式超声波探伤仪,其衰减器性能、垂直线性误差、动态范围、水平线性误差和灵敏度余量应符合条的规定。
5.1.1.2 对比试块的制作与校验方法应符合GB11259的规定。
5.1.2.1 根据钢板厚度选用表1中规定的探头。
表1
钢板厚度mm |
探头型式 |
标称频率MHz |
晶片尺寸mm |
6 — 20 |
双晶直探头 |
5(4) |
直径或边长≥20 |
>20 — 80 |
直探头 |
2.0 — 2.5 |
直径14-30 |
5.1.2.2 双晶直探头性能要求应符合附录A的规定。
5.1.3 对比试块
5.1.3.1 人工对比试块的尺寸见图1和表2
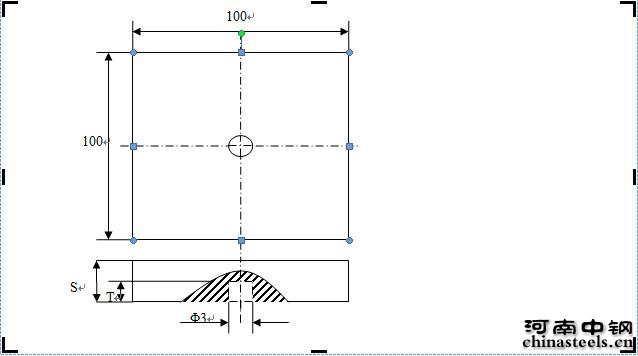
图1
表2 mm
试块厚度S |
平底孔深度t |
6—30 |
1/2S |
>30—60 |
1/3S |
>60—80 |
1/4S |
5.1.3.2 对比试块的制作与校验方法应符合GB11259的规定。
5.1.3.3 试块厚度应与被探钢板相接近,其偏差不应大于板厚的20%。
5.2 探伤方法
5.2.1 扫查方法
5.2.1.1 探头扫查方向原则上应与钢板轧制方向垂直。
5.2.1.2 钢板一般应逐张进行100%面积扫查。
5.2.1.3 当生产厂认为能够保证产品质量时,也可采取间距为50mm的平等扫查。
5.2.1.4 用双晶直探头扫查时,探头分割面应与探头扫查方向呈垂直放置。
5.2.2 扫查速度
5.2.2.1 用直接接触法探伤时,扫查速度应在150mm/S以内。
5.2.2.2 用液浸法(包括局部水浸法和薄层冲水法)探伤,并使用带自动报警装置的仪器时扫查速度最大可到1000mm/S。
5.3 探伤灵敏度
用图1和表2的试块,将平底孔反射波高调至满刻度的50%,并计入对比试块与被验钢板之间的表面耦合差值(dB),作为探伤灵敏度。
5.4 缺陷及其测定
5.4.1 在探伤过程中发现下列显示之一作为缺陷处理。
a、缺陷第一次反射波(F1)波高大于或等于满刻度的50%,即F1≥50%者。
b、当底面第一次反射波(B1)波高未达到满刻度时,缺陷第一次反射波(F1)波高与底面第一次反射波(B1)波高之比大于或等于50%,即B1<100%,而F1/B1≥50%者。
c、当底面(或板端部)第一次反射波(B1)波高低于满刻度的50%,即B1<50%者。
5.4.2 探出缺陷后,应在其周围仔细扫查。对于5.4.1中a和b的缺陷,采用半波高度法测定缺陷边界。
5.4.3 对于5.4.1中c的缺陷,移动探头,使底面第一次反射波高(B1)升到满刻度的50%,此时探头中心移动的轨迹即为缺陷边界。
5.4.4 用双晶直探头测定缺陷边界时,探头移动方向与探头分割面相垂直。
5.4.5 将指示长度大于等于25mm的缺陷记入探伤记录。
5.5 缺陷的评定方法
5.5.1 一个缺陷按其表现的最大长度作为该缺陷的指示长度。当两个或两个以上缺陷邻接在一条直线上而其间距小于相邻缺陷中较小缺陷的指示长度时,则可看作为包括间距在内的连续缺陷,其总和作为单个缺陷的指示长度。
5.5.2 相邻缺陷间距小于等于120mm时,两缺陷面积之和作为一个缺陷面积。
5.5.3 缺陷密集度的评定
5.5.3.1 对于钢板内区求出一平方米面积内指示长度大于等于25mm缺陷的个数,以此进行评定,此时,矩形的短边长度应大于400mm。
5.5.3.2对于钢板周边或坡口预定线,求出任意连续3mm长度内指示长度大于等于25mm缺陷的个数,以此进行评定。
5.5.4 钢板缺陷平均个数的评定
5.5.4.1 整张钢板中,以钢板总面积平均,指示长度大于等于25mm的缺陷个数进行评定。
5.5.4.2 对钢板周边或坡口予定线,以其总长度平均,指示长度大于25mm的缺陷个数进行评定。
5.6 评定标准
缺陷各参数不超过表3、表4时为合格
表3
钢板厚度mm |
单个缺陷最大指示长度mm |
单个缺陷最大指示面积cm² |
密集度
个/m |
钢板总面积缺陷平均度个/m |
6—30 |
100 |
9 |
10 |
1 |
>30—60 |
80 |
16 |
10 |
1 |
>60—80 |
80 |
16 |
15 |
1 |
表4
钢板厚度mm |
单个缺陷最大指示长度mm |
单个缺陷最大指示面积cm² |
密集度
个/m |
钢板总面积缺陷平均度个/m |
四周或坡口 |
50 |
9 |
6 |
1 |
5.7 探伤报告
a、被探钢板情况:钢号、炉罐号、批号、规格和钢板状况等。
b、探伤条件:仪器型号、探头型式规格、试块、耦合剂、探伤方式。
c、探伤结果:将缺陷位置及大小作为示意图,并作出合格与否的评定。
d、操作者、报告签发者、审核者的姓名、技术资格和报告日期等。
附录A
双晶片直探头性能
(补充件)
A1 探头性能
A1.1 距离—波幅特性曲线
用ZB Y231规定的DB-D1试块,在各个厚度上测定其回波高度(dB),作出如图A1所示的特性曲线,该曲线应下述要求:
a、 在厚度19mm上的回波高度,与最大回波高度差应在3dB~-6dB的范围内。
b 、 在厚度3mm上的回波高度,与最大回波高度差应在3dB~-6dB的范围内。
A1.2 表面反射波高度
直接接触法测得的表面反射波高度,应比最大回波高度低40dB以上。
A1.3 检出灵敏度
图A2试块平底孔反射波高度,与最大反射波高度差应在-10dB±2dB的范围内。
A1.4 有效声束宽度
探头置于A2试块平底孔上,顺探头分割面方向移动,测定最大反射波位置,再向两侧移动到降低6 dB的范围,为有效声束宽度,其值应不小于15mm。
图A1 距离—振幅特性曲线
图 A2
中华人民共和国国家军用标准
FL 9515 GJB 1496A—2000
装甲用28Cr2Mo、26SiMnMo和
22SiMn2TiB钢板规范
2004—04—24发布 2000—09—07实施

中国人民解放军总装备部 批准
附录B
超声波检验方法(补充件)
B1 主题内容与适用范围
B1.1 主题内容
本附录规定了装甲用转炉28Cr2Mo、26SiMnMo、22SiMn2TiB钢板超声波检验方法、缺陷评定、验收标准、报告与标志等。
B1.2 适用范围
本附录适用于装甲用28Cr2Mo、26SiMnMo、22SiMn2TiB钢轧制厚度为10mm~30mm钢板。
B2 一般规定
B2.1 本附录规定的脉冲反射式纵波直声波检验方法能够检查出平行于钢板轧制表面的破坏金属连续性的缺陷,例如:分层、非金属夹杂、气泡等。
B2.2 钢板在轧制或热处理状态下进行检验,钢板表面应清洁、光滑、不应有影响检验的氧化铁皮、锈蚀、油污等。
B2.3 藕合剂可用油或水,采用局部水浸法检验时,检验用水应清洁,清除影响检验灵敏度的气泡、杂质等,水温以5°C~40°C为宜。
B3 探伤仪及探头
B3.1 探伤仪应符合ZBY 230的规定。
B3.2 探头可采用单晶探头,或双晶直探头,晶片直径为φ20mm~φ25mm或面积相当的矩形晶片。
B3.3 允许采用其它形式的探头进行缺陷评定及缺陷定位。
B4 检验方法
B4.1 可采用直接接触法、局部水浸法或液柱藕合法。
B4.2 检验频率可根据钢板厚度、晶粒度、微观组织、仪器性能等,选用频率为2MHz~5 MHz。
B4.3 检验灵敏度为钢板完好区第一次底面回波幅度等于满幅的50%~90%。
B4.4 探头扫查可在钢板任一轧制面上进行,沿垂直于钢板轧制方向作平行扫查,扫查间距为75mm,并沿钢板公称尺寸四周50mm以内进行复加扫查。
B5 缺陷评定方法
B5.1 评定缺陷灵敏度与检验灵敏度应一致。
B5.2 下述缺陷为记录缺陷
a、无底在面回波,只有缺陷回波的多次反射。
b、缺陷回波波幅等于或大于第一次底面回波波幅的50%或使用底面回波波幅降低50%的所有缺陷。
B5.3 缺陷面积的确定
移动探头并记录底面回波与缺陷回波相等时的探头中心点,连接各点所围成的范围,即为缺陷面积。
B6 验收标准
B6.1
I级
在任何区域,如发现一个或多个回波消失,同时在同一深度上有连续的缺陷回波,而这些缺陷能被直径为75mm的圆包围时。
B6.2 II级
钢板上存在B5.2a规定的不能为75mm直径圆包围的缺陷。
B7 报告与标志
B7.1 检验操作应由持有有关部门认可的超声检验II级技术资格证书的人员或在II级人员指导下的I级人员承担,但签发报告应由检验II级或II级以上人员负责。
B7.2 检验操作必须有原始记录。
B7.3 按本方法检查合格的钢板应在钢板打字端用钢印打清验收标准的合格级别,即I级标志为“UT-1”,II级标志为“UT-2”。
钢铁产品对厚度≥6mm钢板的超声波检验
质量定义———检验方法
(法国标准)
NF A04——305
1983年5月
前 言
采用较宽网格的超声波检验不能系统地探测出所有缺陷,它只能给出缺陷出现的频繁度及严重程度的大概值。然而,经验表明,不必对钢板进行100%的检验以判断质量水平。
因此,凡是钢板的最终使用不允许接受由采用本标准所允许的缺陷时,就应采用其他检验技术。
1 目的
本标准描述对厚度≥6mm的非合金或合金钢板的内部缺陷进行超声检验的方法。而且还根据制订的准则按质量升级的顺序规定出三种质量等级:A级、B级、C级。
2 适用范围
本标准适用于标称厚度≥6mm的非合金或合金钢的无涂层钢板,不包括奥氏体钢或奥氏体合金钢。
然而,经事先同意 后,本标准可适用于奥氏体钢或奥氏体合金钢;但条件是:电噪声电平必须低于所采用的方法的探测临界值的振幅。本标准中规定的验收准则不适用于超声波穿透法检验。
3 参考资料
A09——300 无损探伤——超声波检验专业词汇
A09——320 金属产品超声波检验手册设备性能审核部分
4 方法
4.1 方法原则
所采用的方法根据纵向形式的超声波的反射原理,其平均方向垂直于探头表面。检验包括:
(a) 缺陷检查:比较缺陷反射信号的高度,与缺陷同深度处给定直径的平底孔的反射信号高度。
(b)缺陷界定:缺陷的范围由探头中心连续位置界定,此时缺陷反射信号高度等于最大高度的一半。(6dB)
对所有厚度钢板的探测应在超声波第一行程中执行
4.2 设备
4.2.1说明
探测设备应有一个波器屏幕,能够跟踪通过材料的超声波,并且根据试验标准A09——320进行过校核。放大刻度以分贝为单位扫描的功率及速度(以时间为基准)应能在较大范围内可调节。设备应至少有一个探头,它可以是垂直的单晶探头用于发射及接收,或者是一个双晶探头。考虑到发射及接收时的波是纵向形式,其平均方向几乎垂直于钢板表面。
探头的频率及尺寸应能保证在检验范围内灵敏度。直探头的盲区应尽可能小,且不得大于10mm。双晶探头的江聚区应按钢板厚度进行调整。
使用的探头的标称频率应在2—5MHZ之间,且晶片尺寸应在10——25mm之间。探头的选用应依照钢板厚度而定,具体见下表:
钢板的标称厚度 |
探头的类型 |
e≤20mm |
非零度倾角的双晶探头 |
20mm<e≤60mm |
零度倾角的双晶探头 |
e>60mm |
直探头 |
探头可以手持或安装在一个连续探伤系统上,缓慢移动,使缺陷容易识别出来,要考虑到屏幕余辉效应或缺陷信号装置的响应时间。若是双晶探头,其两个晶片间的隔声层应垂直于探头移动方向。
4.2.2探头的特性曲线
对于每个探头,应确定出以下特性曲线:3
——测出不同板厚的底面回波高度变化的曲线(见图1中的曲线1)。
——测出一下直径的平底孔,在不同深度时回波高度变化的曲线(见图1中的曲线2)。
直径11mm(Φ11)(对应面积为100mm²的缺陷)适用于A级
直径8mm(Φ8) (对应面积为50mm²的缺陷)适用于B级
直径5mm(Φ5) (对应面积为20mm²的缺陷)适用于C级
当用双晶探头进行检验时,对于所有级别,只有使用5mm直径(Φ5)的孔。因为相应于8mm及mm直径孔的特性曲线与底面反射回波曲线非常接近。
应采用试块确定这些曲线(阶梯试块用于测底面回波高度变化曲线;具有不同深度的平底孔的方试块用于测直径为11mm、8mm、5mm的特性曲线。且试块尺寸大小应使得没有侧壁效应)。试块应由组织均匀的碳钢制成。每条曲线至少应在探头适用范围里取5点确定。
4.2.3 设备的调节
设备在使用前的调节,具体涉及到扫描速度,功率及放大率的确定。
扫描速度的调节应使得示波器上传输回波与底波回波之间的距离是以清晰地显示出缺陷回波。
功率及放大率的调节,应在无任何缺陷的完好区域上同时进行。
然后将第一次底面反射波调到底面反射回波曲线上,反射波高度的调节通过功率及放大率的同时调节进行,在检查中,选择出能使盲区达到最小的那种状态。探测中建议应尽可能保持一个单个功率值,这是由于4.2.2中规定的放大率设定值允许在屏幕极限内评价缺陷。
4.3 耦合条件———钢板的表面状态
耦合介质应保证在探头与钢板表面之间有足够的声传输。通常采用水,但也可采用其他介质(油、浆糊等)。
通常在检验时不需对钢板表面特别准备,但被检验的表面硬物粘着氧化物、灰尘、油污等影响耦合条件的外来物。表面状态应当是在没有内部缺陷的区域,至少能区分出两个连续的底面回波,且其波高不小于对所检厚度的底面回波的特性曲线的波高。
5 检验条件
5.1 总则
在检验时,扫描形式如5.2.1及5.2.2所述。钢板检验仅在一面进行。当能够判断钢板是否符合要求之后,即可停止操作。
超声波检验应在生产厂,由生产厂根据规定由取得三级检验员资格,或由等同认可资格的检验员进行。当合同中有规定时,可在用户或其代表在场时进行检验。
5.2扫描方式
5.2.1 A级钢板
扫描方式应在合同中详细写出,应当包括:
(a)钢板四周检验:即沿钢板交付尺寸的所有4个边缘的带状区域探测,带宽等同于板厚,最小为50mm。
(b)钢板本体检验:①即先按(a)款进行钢板四周检验。②后续检验;沿着平行于钢板边缘的200mm见方的方格的各边进行;或者沿着在表面上均匀分布的线,给出相同的检验程度。
5.2.2 B级和C级钢板扫描方式包括:
(a) 钢板四周检验:沿钢板交付尺寸的所有4个边缘的带状区域探测,带宽为板厚的1.5倍,最小为50mm。
(b)钢板本体检验:沿着与钢板边平行的100mm的方格的各边进行。或沿着在表面上均匀分布的线,给出相同的检验程度。
对于C级钢板,根据草图,对于要焊接的区域,在合同上由协议规定出与钢板四周上的扫描相一致的扫描方式。
5.2.3 经事先同意,可以规定其它的扫描方式。
5.3操作方式:
应根据4.2.3对设备进行调节,按选定的扫描方式进行扫描,首先定出缺陷位置,接着确定其大小。
5.3.1 缺陷的探测
对于给定厚度的钢板,此方法为:将底面回波高度调到“底面反射高度变化曲线”上的某值,并根据所选定的级别,将缺陷回波高度与特性曲线(直径11.8及5mm)相比较。只有缺陷回波高度大于特性曲线的高度时,才将其定义为缺陷。
5.3.2 缺陷大小的确定
5.3.2.1 整张钢板的检验
5.3.2.1.1 使用双晶探头进行检验
应将所有发现的缺陷界定其尺寸,缺陷范围由探头中心位置决定.缺陷范围由缺陷反射波高度等于其最大高度的一半来确定(即6dB法).这种确定缺陷范围的工作应采用同一探头或具有相似特性曲线的探头来完成,发现缺陷时将其标出.
缺陷的界线确定了缺陷的表面积S,两处处相邻的缺陷,当其间距小于或等于两者间小者的长度时,这两处缺陷应被视为连续的,其表面积这这两处缺陷表面积之和.
5.3.2.1.2使用单直探头进行检验
检验包括:
——对于A级钢板。按5.3.2.1.1中规定的6dB法确定缺陷边界。
——对于B级和C级钢板:采用Φ5、Φ8、Φ11平底孔的特性曲线来确定缺陷个数,这种计数应在检验期间进行。
具体确定缺陷个数方法如下:
——对于B级:确定出回波高度大于Φ11平底孔特性曲线的缺陷个数以及回波高度在Φ8和Φ11特性曲线之间的缺陷个数NB。
——对于C级:确定出回波高度大于Φ8平底孔特怕曲线的缺陷个数以及回波高度在Φ5和Φ8特性曲线之间的缺陷个数NC。
5.3.2.2 钢板四周检验
检验包括对钢板四周的带状区域的整个表面进行扫查,检验条件与钢板本体的检验条件相同;钢板四周的带状区域按5.2.1和5.2.2中规定执行.
发现缺陷时,可按其最大表面积(S)命名,也可按其平等于边缘方向上的最大长度(L)命名.这些缺陷的界定用6dB法确定.
5.4验收准则
表1a及表1b给出了使用不同类型探头时三种质量等级(A级、B级、C级)的验收准则。按照合同规定,钢板交付时可以是钢板本体与四周边缘处于不同等级。
6 文件
生产厂应担供一份符合本标准的证书。
如果合同中有规定,应将包括有以下内容的探伤报告提供给用户:
——被检验钢板的参数。
——探头特性及设备的类型。
——使用的操作条件(耦合剂、扫查形式等)
——检验结果
注释:
(1)合同同意可以具体规定出,底面回波消失而无中(缺陷)反射波出现的情况。
(2)见A09—300标准。
(3)当钢板组织要求时,也可采用较低的频率。在此情况下,可以使用较大直径的探头。
(4)按草图要求焊接的区域。
表1a 采用双晶探头进行检验的验收准则
级别 |
不可接受的分散缺陷 |
不可接受的群集缺陷 |
缺陷大小 |
最大密度不大于 |
A |
本
体 |
S>1000 m㎡ |
100<S≤1000m㎡ |
—在最密度集处的200mm见方区域内:4个
—在最密集处的1mm见方区域内:15个 |
边
缘 |
L>30mm或S>1000 m㎡ |
100<S≤1000m㎡ |
—在最密集处的1m长度内:3个 |
B |
本
体 |
S>100 m㎡ |
50<S≤100 m㎡ |
—在最密集处的100mm见方区域内:2个
—在最密集处的1m见方区域内:10个 |
边缘 |
L>20mm或S>100 m㎡ |
50<S≤100 m㎡ |
—在最密集处的1 m长度内:2个 |
C |
本
体 |
S>50 m㎡ |
20<S≤50 m㎡ |
—在最密集处的100mm见方区域内:2个
—在最密集处的1m见方区域内:5个 |
边缘 |
L>15mm或S>50 m㎡ |
20<S≤50 m㎡ |
—在最密集处的1 m长度内:2个 |
① 草图上要求的焊接区域 |
表1b 用单直探头进行检验的验收准则
级别
|
不可接受的分散缺陷 |
不可接受的群集缺陷 |
缺陷大小 |
最大密度不大于 |
A |
本体 |
S>1000m㎡ |
100<S≤1000m㎡ |
—在最密集处的200mm见方区域内:4个
—在最密集处的1m见方区域内:15个 |
边缘 |
L>30mm或S>1000m㎡ |
100<S≤1000m㎡ |
—在最密集处的1m长度内:3个 |
B |
本体 |
波高大于Φ11平底孔特性曲线的缺陷 |
NB
(直径介于Φ8和Φ11之间) |
—在最密集处的100mm见方区域内:2个
—在最密集处的1m见方区域内:10个 |
边缘 |
L>20mm或S>100m㎡ |
50<S≤100m㎡ |
—在最密集处的1m长度内:2个 |
C |
本
体 |
波高大于Φ8平底孔特性曲线的缺陷 |
NC
(直径介于Φ5和Φ8之间) |
—在最密集处的100mm见方区域内:2个
—在最密集处的1m见方区域内:5个 |
边缘 |
L>15mm或S>50m㎡ |
20<S≤50m㎡ |
—在最密集处的1m长度内:2个 |
①草图上要求的焊接区域 |
西气东输用钢板(X70)探伤标准
XQ13-2000
西气东输用钢板(X70)的探伤,是按照中国石油天然气股份有限公司西气东输管道分公司,发布的Q/SY XQ13-2002技术条件进行。Q/SY XQ13-2002技术条件中有关探伤的内容如下:
9.4无损检测
9.4.1.1所有钢板均应进行目视检查和超声波检查,以检测钢板表面和内部分层缺陷。
9.4.1.2超声波检测耦合方式可选择:接触法、液浸法和局部液浸法。
9.4.1.3在生产之前应将钢板超声波检测方法用书面形式提交给购方。
9.4.1.4检测结果应有正规报告,并作为正式检验报告提供给供方。
9.4.2超声波检测技术要求
9.4.2.1仪器及设备
9.4.2.1.1所使用的超声波设备应是脉冲回波反射式仪器,自动化超声波检测系统应配有喷标、声光报警系统,用以发现缺陷及监视探头与钢板表面之间的耦合情况,并具备记录功能。应提交检测及仪器校验技术规范,特别是对于动态工作和校验方式中所发现的缺陷、位置进行确认,并将确认方法提交给购方。
9.4.2.1.2探头:探头晶片直径或边长小于30mm,也可选择有效声束面积至少为450mm²的其他探头,频率推荐使用2.5MHz、2.25MHz,在评估和精确定缺陷时,允许所有其它探头。
9.4.2.1.3耦合剂:机油、水或其他有效耦合介质。
9.4.2.2对比试块
9.4.2.2.1采用钢板上钻出的圆形平底孔作为校准对比试块,她是用于校准仪器和检测系统的标样。对比试块人工缺陷的尺寸不应理解为这些设备所能检测缺陷的最小尺寸。
9.4.2.2.2对比试块与被检钢板应具有相似的表面状态和声学性能。
9.4.2.2.3对比试块尺寸为:
平底孔直径:6(0,+0.35)mm
平底孔深度按下述要求:
钢板厚度,mm |
平底孔深度 |
17.5 |
T/2 |
21.0 |
10mm |
26.2 |
T/4 |
30.4 |
T/4 |
9.4.2.2.4对比试块人工缺陷几何尺寸应由专门计量机构测量检定。
9.4.2.3仪器及系统校准和校验
为证实检测设备及检测程序的有效性,检测系统/仪器采 用对比试块或经购方认可的其他对比试块进行校验。
9.4.2.3.1静态校准:静态下以对比试块上的平底孔产生的信号 100%幅度作为设备设定的触发/报警界限。
9.4.2.3.2动态校准:采用人工或其它方式移动对比试块或探头,移动速度应大于或等于正常检测速度调节设定灵敏度,使探头均能检测出对比试块人工缺陷,且能触发报警系统。
9.4.2.3.3校验频次:校验频次为每4小时或每检测10张钢板校验一次(以时间较长者为准),但当交接班或操作人员更换时检测设备也应校验。
9.4.2.3.4生产过程中,若发现检测仪器或系统不满足校准要求,而且将灵敏度提高3dB后仍不能满足校准要求,则上次校验后检测过的所有钢板应在重新校准后进行检测。
9.4.2.4检测扫查方式
超声波自动化检测系统可依照ASTM A435标准规定选择扫查方式,扫查至少能覆盖钢板表面的25%。如在线超声波检测存在盲区,则至少纵向板边50mm、板端300mm范围内应用人工超声波检测或其它有效检测方式进行检测。
9.4.2.5验收
9.4.2.5.1未产生触发/报警的钢板判为合格。
9.4.2.5.2产生触发/报警的钢板应视为可疑,应按本技术条件重新进行复验,如复验中未产生触发/报警,则应判为合格钢板。产生触发/报警的钢板,则认为该钢板可疑。
9.4.2.5.3对可疑钢板可疑区域,应采用手动超声波检测方式,确定分层的位置、范围和大小,按8.6规定进行处理。
附录:Q/SY XQ13-2002技术条件中8.6条规定
8.6 分层
钢板端头及纵侧边上不允许存在分层。
钢板端部及纵侧边25mm范围内的分层均是为缺陷,有这种缺陷的钢板应切除,直到除去这种分层为止。
其它部位上的允许分层的界限值为:
任何方向不允许存在长度超过50mm的分层;长度在30mm~50mm的分层相互间距应大于500mm;长度小于30mm、相互间距小于板厚的若干小分层构成连串性分层,该连串性分层中的所有小分层长度总和不得大于80mm。
超声波检验钢板、带材和扁材内部缺陷的
验收等级规范 BS5996:1993
1、适用范围
本英国标准规定了用超声波检验铁素体和奥氏体钢板,带材和宽扁材料内部缺陷的验收等级。6个验收等级(B1——B6)适用于材料的本体,3个验收等级(E1——E3)适用于材料的边缘。还为奥氏体钢板规定了两个验收等级,一个用于材料本体(B7),另一个用于材料边缘(E4)。
本英国标准包括用人工、辅助人工,半自动或自动检验方法检验厚度范围在5mm——200 mm的材料。本英国标准可用于指定用于生产焊管的钢板、带材的超声波检验,可根据验收等级B1——B4和E1——E3探测内部缺陷。
注1:当确定材料用于关键用途,以及对于某些等级的奥氏体钢种,可由买方规定那两个特殊的验收等级,一个用于材料本体,加一个用于材料边缘(分别如BX和EX )。当规定这些验收等级时,买方和生产厂之间应协商检验灵敏度和将要采纳的参考标准,以及缺陷大小和总体密度的验收标准。
注2:依照本英国标准提供的材料可符合任何用于材料本体或材料边缘的验收标准,或用于材料本体和边缘的任何组合的验收标准,例如:B3、E2、B3E3、B3E2。
注3:对于厚度小于5mm和大于200 mm(或对于由化学成分决定的奥氏体钢板,厚度小于200 mm的钢板,用超声波检验来探测内部缺陷可能要经历一些困难。在此情况下,要求买方和生产厂之间进行协商,以确定任何与本英国标准不符之处。
2、标准参照
本英国标准参考了其它出版社的规定版本中的条款。在本文适当的地方引用了这些参照标准,在封底内侧列了出版社。对这些刊物随后做的修正或其修订本,只有在本英国标准引入修正或修订本时,才适用于本英国标准。
3、定义
对于本英国标准,在BS3683第4部分:1985及下列条款中给出定义。
3.1内部缺陷
在材料厚度范围内的任何缺陷,例如,平面或层状缺陷,单面或多面夹杂带或群。
3.2缺陷
有能接受的内部缺陷,例如,超过规定的最大尺寸或总体密度极限。
3.3总体密度
在规定的每个单位边缘带长度或每个单位本体面积内,尺寸大于一个规定的最小尺寸,和小于一个献宝的最大尺寸的单个内部缺陷数量。]
3.4人工和辅助人工检验
由操作人员把一个超声波传感器(即超声波探头)或几个传感器置于材料表面,在材料表面用人工制作适当的探头扫描线,通过直接观察或安装在内部的信号振幅报警装置,用肉眼评定超声波探伤仪屏幕上的超声波信号指示。
3.5自动和半自动检验
用机械方法把1个超声波传感器或多个传感器置于材料表面,制作适当的扫描线,通过电子手段评定超声波信号指示。这种检验可以是全自动的,不需操作人员参与,或当操作人员执行基本的设备操作功能时,也可以是半自动的。
4.验收等级
4.1材料本体验收标准B1——B7的规范由表1给出(还可见图1)。当依照附录A检验时,如果材料满足下列要求,就应认为是符合一个特殊的验收标准。
(a)材料中不应有大于表1中给出的最大的单个缺陷尺寸Bmax
(b)小于最大缺陷尺寸但大于最小缺陷尺寸的缺陷的总体密度不应大于表1中的规定。
注:对于大于最小缺陷尺寸的一个缺陷,必须超过表1中给出的最小面积,最小长度和最小宽度。
4.2材料边缘验收等级标准E1——E4的规范应在表2中给出(还可见图1)。当依照附A检验时,如果材料符合下列要求,就应认为是符合一个特殊的验收等级。
(a) 材料中不应有大于表2中给出的最大单个缺陷面积Emax的内部缺陷。
(b) 小于最大缺陷长度,但大于最小缺陷长度的缺陷的总体密度不应大于表2中的规定。
4.3如果材料不符合一个特殊的验收标准,则必须采取下列步骤。
(a) 应去除可疑面积,只要边缘符合适用的验收标准,则应认为剩余面积是可以接受的。
(b) 该材料应报废.
表1 材料本体检验验收规范
验收等级 |
最大单个缺陷面积B maxmm2 |
考虑的最小缺陷尺寸(见注1和注2) |
小于Bmax`大于最小缺陷尺寸的缺陷的最大总体密度 |
最大扫描线间距S
mm |
面积mm 2 |
长度mm |
宽度mm |
每1m×1 m平方的缺陷数量 |
每500mm×500 mm平方的缺陷数量 |
B1 |
10000 |
2500 |
100 |
20 |
5 |
_ |
100 |
B2 |
5000 |
1250 |
75 |
15 |
5 |
_ |
75 |
B3 |
2500 |
750 |
60 |
12 |
5 |
_ |
60 |
B4 |
1000 |
300 |
35 |
6 |
10 |
_ |
35 |
B5 |
500 |
150 |
15 |
6 |
_ |
10 |
15 |
B6 |
100 |
30 |
5 |
5 |
_ |
5 |
151) |
B71) |
50 |
25 |
5 |
5 |
3) |
_3) |
151) |
(1) 对于验收标准B6和B7,给出的最大扫描线间距是以以使用一个直径为25mm的探头为基础.在使用较小探头时,最大扫描线间距应是探头的75%.
(2) 只用于奥氏体钢板.
(3) 买方和生产厂之间应协议对验收标准B7的缺陷总体密度的要求。
注1:对一个大于最小缺陷尺寸的缺陷,必须均超过表1中给出的最小面积,最小长度和最小宽度。长度是和扫描轨迹呈直角的尺寸,宽度是平行于扫描轨迹的尺寸(见图1)。
注2:为了确定可疑面积的范围,当两个相邻缺陷的间距小于这两个相邻缺陷中的短轴较小者时,这两个相邻缺陷应作为一个缺陷考虑。
注3:验收等级B
x还可用于材料本体检验。该等级的验收规范应则买方和生产厂之间协议。
材料边缘检验的验收规范 表2
验收等级 |
最大单个缺陷尺寸 |
考虑的最小缺陷长度Lminmm |
最大总体密度(每1m长度上小于最大缺陷尺寸,大于Lmin的缺陷数量 |
长度Lmaxmm |
面积Emaxmm2 |
E1 |
50 |
1000 |
30 |
5 |
E2 |
30 |
500 |
20 |
4 |
E3 |
20 |
100 |
10 |
3 |
E4 |
10 |
50 |
8 |
2 |
(1)只用于奥氏体钢板。
注1:E
max是纵向尺寸L
max和横向尺寸的乘积,如果超过E
max或L
max,就认为这个缺陷大于最大缺陷尺寸。
注2:长度是平行于材料边缘的尺寸。
注3:为了确定可疑的面积范围,当两个相邻缺陷的间距小于两个相邻缺陷中的短轴较小者时,这两个相邻缺陷应作为一个缺陷考虑。
注4:验收等级E
x还可用于材料边缘检验。该等级的验收规范应由买方和生产厂之间协议。
附A (标准)
钢板、带材和宽扁材的超声波检验方法
A.1 总述
A.1.1检验阶段
超声波检验应在轧制状态或在热处理后交货的材料上进行。
A.1.2 人员
检验应生产厂指定的,具有认可的合格资格证书的人员执行。
注:资格证书的确认由生产厂和买方协商。
A.1.3 表面状态
材料应足够以保证检验有效。表面可能有氧化铁皮、脏物、油脂、涂料和其它干扰检验的有效性的外来物质。
A.2 装置
A.2.1 总述
A.2.1.1 用于人工和辅助人工检验的超声波设备应是脉冲回波型的,依照BS4331:1部分;1978的3部分;1974性能和校对检验为准。
A.2.1.2 用于自动和半自动检验的超声波设备应能够通过自动触发器\报警器区分可接受的和可疑的材料。
注1:这种区分可以结合对最大允许尺寸缺陷和密集缺陷等内部缺陷面积的评估来实施。可能时要结合标识或分类系统。
注2:在超声波检验之前,自动和半自动设备的性能应由生产厂证明能令买方满意,它能够探测到要求的最小尺寸的缺陷。
A.2.1.3 应使用一种能传导超声波探头和将要检验的材料表面之间的超声波的一种液体介质(例如:水或油)。介质不应对材料或其表面光洁度有有害影响。
A.2.2 超声波探头
A.2.2.1 应使用一个公称角度为0º的超声波压缩波传感器。
用于自动和半自动检验的超声波传感器应是单探头或双探头型。
用于人工和辅助人工检验,超声波探头的类型应如表A.1中规定。
用于人工和辅助人工检验的超声波探头类型
表A.1
材料厚度t mm |
探头类型 |
5≤t≤20 |
双 |
20< t≤100 |
单(1)或双 |
100< t≤200 |
单(1) |
(1) 当使用一个单探头时,应采用下列之一:
(a) 在实际应用中,近表面的死区不应超过规定的材料厚度的15%或15 mm,或两者中较小者。
(b) 若在(a)中规定的近表面死区不实际的话,应在第一和第二个底波之间进行检验(见A.4.3)或从材料两侧检验。
A.2.2.2 除非由于材料结构而使材料表现出较高的超声波衰减特性(例如:一些奥氏体钢种或厚型材上),否则,最小的超声波检验频率应该是2MHZ。
注:如果材料表现出高超声波衰减特征,可以使用一个高超声波衰减特征的材料,生产厂应告知买方。
A.2.2.3 除非由于材料结构使表现出较高的超声波衰减特征(例如,一些奥氏体钢种或厚型材上),超声波探头的最大尺寸应是25 mm。
注:如果材料表现出较高的超声波衰减特征,可以使用一个较大的超声波探头。
如果打算把一个较大的超声波探头用于表现出较高超声波衰减特征的材料,生产厂应告知买方。
A.3 过程
A.3.1 总述
使用下列检验方法之一
(a) 只检验材料的一个表面,用超声波脉冲回波技术探测内部缺陷,超声波通常在垂直于检验表面的方向上透射。
(b) 如果由于材料结构使材料表现出较高的超声波衰减征(例如,一些奥氏体钢种或厚型材上),利用超声波脉冲回波技术,从材料两侧检验(如(a)所述)。在该情况下,生产厂应能够证明从每一侧检验了厚度超过50%的材料。
(c) 利用自动超声波透射技术检验材料,可证明其效果等同于(a)中所述的超声波脉冲回波技术。
A.3.2检验材料本体
A.3.2.1 在人工和辅助人工检验材料本体时,以不超过150mm/s的速度,彼此相对地移动材料和探头装置,沿着和主轧制方向呈直角的平等的等距扫描线,扫描材料表面,以保证探测出具有极限长度和宽度尺寸的相关的最小尺寸的缺陷(见表1)
最大扫描线间距应如表1中所示。
A.3.2.2 在自动和半自动检验材料本体时,彼此相对地移动材料和探头装置,这样沿着等距的扫描线扫描材料表面,以保证探测到具有极限长度和宽度尺寸的相关的最小尺寸的缺陷(见表7)。
相对于沿扫描线相对移动的每个探头的脉冲重复频率应足以保证探测有关的最小长度和宽度尺寸的缺陷(见表1)。
A.3.3 检验材料边缘
在检验材料边缘时,彼此相对地移动材料和探头装置,这样从最后切边定位的整个区域内能100%地扫描材料表面。为了探测有关的最小缺陷长度L
min(见表2),该区域的宽度应如表2所示。
注:纵边是平等于主轧制方向的边,横边是和主轧罅方向呈直角的边。
表A.2 用于材料边缘检验的区域宽度
材料厚度t mm |
区域宽度 mm |
5≤t≤33.3 |
50 |
33.3< t≤66.6 |
1.5 t |
66.6< t≤200 |
100 |
A.4 检验灵敏度
A.4.1 静态调整超声波设备和传感器,确定检验灵敏度如下:
(a) 仅对于验收等级B1——B4和E1——E2调整设备灵敏度,在材料的完好部位上得出的第一个底波波高在荧光屏上的100%;或
(b) 对于验收等级B5和其以上的等级,依据附B,利用有关的距离振幅修正(DAC)曲线,参考试块,确定设备灵敏度。或
(c) 对于自动和关自动检验设备,保证在检验灵敏度上,设备将探测到在静状态下标准试件中适当的参考目标。
A.4.2 对于验收标准B5——B7,E3的E4,用一个直径5mm的平底孔作参考目标。
注:对于验收标准B
X和E
X,买方和厂方应协议参考目标的直径。
A.4.3 除非表A.1中另有规定,调整超声波设备,使超声波全厚度扫描在入射面和底面之间进行,以便在这段时间内清楚地识破来自内部缺陷的信号响应.
A.4.4 当使用DAC曲线时,调整检验灵敏度,在准备DAC曲线时,通过检验用试块和检验材料之间衰减率的差别,确定灵敏度,要考虑到材料厚度。。
A.4.5生产试验相同厚度和缸中的材料过程中,要定期校验设备的检验灵敏度。校验设备的检验灵敏度的周期应至少每8小时1次。
A.4.6在任何系统更换或当规定的公称材料厚度或钢种改变时,要重新调整设备检验灵敏度。
A4.7如果在生产试验过程中,甚至在提高灵敏度2dB并允许系统漂移后,发现检验灵敏度不能令人满意;则灵敏度检测前,所有检验的材料应在设备检验灵敏度重新调整以后重新检验,除非备有从单个可识别材料中得出的记录数据,能够准确地分出可疑的和可接受的两类。
A.5 缺陷规范
A.5.1 等级B1——B4和E1、E2存在的内部缺陷有下列几条指示:
(a)有或没有一个缺陷回波的存在,底波的信号振幅减少50%;
(b)一个缺陷波使底波下降50%或超过50%。
A.5.2等级B5及B5以上和E3及E3以上存在的内部缺陷有以下指示:
(a)有或没有缺陷回波,底波的信号振幅减少50%。
(b)存在一个缺陷回波,等于或超过相同深度的一个参照目标的响应,即:等于或超过DAC曲线。
注:在要求检验灵敏度较高的材料上,第一个底波信号可以是饱和状态。在此情形下,有必要用降低的灵敏度再进行一次扫描,以检验(a)中所述的缺陷。
A.5.3 缺陷的评定
如果探测到任何缺陷,可通过下列方法评定每个区域的缺陷:
(a) 依据附C,通过人工技术确定那个面积内的缺陷大小和夹杂物密度;或
(b)利用一个能被证明能准确地描绘缺陷的自动系统。
A.6 检验报告
当要求时,厂方应向买方提交一份检验报告。最低限度应包括下列信息:
(a) 材料(钢种、熔炼号)识别和尺寸;
(b) 材料状态(例如:轧制、正火);
(c) 探头型号、尺寸和频率;
(d) 检验设备型号和模式;
(e) 使用的介质;
(f) 扫描模式;
(g)与本英国标准的有关验收等级相一致的报告;
(h)操作人员的身份(UT)资格证书)。
附B 用于建立一个距离振幅修正(DAC)曲线的技术
B.1 原理
在该技术中,在声波入射面下,同一材料深度上比较从一个内部缺陷返回的能量和从一个参照返回的能量。
通过选择一个适当的参照目标,确立一个临界信号响应曲线,内部缺陷在该曲线处变得明显并将随之开始规定的变化。
对照目标通常是一个平底孔,但是,只要选择的凹口的长度和宽度能提供一个基本上等于利用同样设备传感器类组合,从规定的平底孔得到的超声波信号,也允许使用三角形凹口。
该技术要求提供一个专门准备的接近被检验材料厚度的检验用试块,在不断加深的材料深度上,该试块包含一系列的直径相同的平底孔目标。
B.2 检验用参考试块
注:在实际应用中,检验用试块应具有和检验材料基本相似的声波性能。入射表面应平直,内部没有经常出现的可识别的超声波响应的内部缺陷。如果检验用试块的衰减系数明显不同于被检验的材料,则应采用灵敏度补偿(见A.4.4)。
检验用试块的外部尺寸,长度和宽度应由厂方选择,以便参照目标能满足彼此和从检验用试块的端面及棱边分开,以避免相互开挠,这样就可以从每个参照目标上得到一个清晰地可分辨的信号指示。检验用试块的较低表面,便于采用参照目标。
对于优质钢种B5——B7,E3和E4,平底孔参照目标的直径应是5mm。
注:对于优质钢种BX和EX,买方和供方之间应协议平底孔参照目标的直径。
使用的平底孔的直径和凹口的宽度公差应是±5%。每个参照目标的底部应是标准平直的,平行于超声波入射面(在2%以内),且没有能明显地降低其超声波反射能力的凹坑或划痕标志。参照目标的边侧应垂直于超声波入射面。
B.3 DAC曲线的结构
对检验用规块中的每个对照目标的响应作一个最初的评定,以确定哪个参照目标给出最大响应。
用经过最大响应的参照目标而优选的探头,调整设备增益/衰减器控制,设定回波高度大约为整个荧屏高度的80%。在荧屏上标出回波尖端的位置,记录增益/衰减器值。
该增益调整是检验灵敏度。
在记录的增益/衰减器值中,优选检验用试块中每隔一个参照目标上的传感器,反过来,对于每个目标,要标出回波尖端在荧屏上的位置。
在荧屏上画一条连接标出点的缺陷探测器的曲线。该曲线是DAC曲线,不包括检验用规块/缺陷探测器/传感器组合使用在内。在使用其它组合时,应建立独立曲线。
附C 通过人工超声波扫描测定内部缺陷的大小
C.1 总述
人工超声波脉冲回波扫描测定钢板、带材、宽扁材内部缺陷大小的过程在C.2中叙述。
该过程采用已知的6dB衰减法或半波法,以这一事实为基础,即当半个超声波声束击到一个内部缺陷时,缺陷回波振幅从最大的缺陷回波振幅上减小了6dB。
该方法能准确地描绘等于或大于探头面积的一个缺陷。对于较小的缺陷,该方法在一定程度上将缺陷尺寸放大。
该方法适用于描绘表1中的验收标准B1-B5和表2中E1-E的缺陷尺寸。
对于验收标准B6、B7、BX、E4和EX,可以采用该方法,但是缺陷尺寸放大会造成不准确。在这些情况下,可使用其它适用的测尺寸技术。
C.2 过程
将探头置于缺陷上反复扫描以获得最大的回波振幅.调整增益值,以便使信号振幅位于整个荧屏高度的40%到80%之间。记下实际高度。把增益值提高到6dB,在缺陷边缘上方移动传感器,直到缺陷回波降至记录的荧屏高度。然后,缺陷的边缘和传感器的轴重合。在很多方向上重复该动作,这对描绘缺陷边缘很有必要。当使用双晶传感器时,双晶体的隔声层应和缺陷的周边呈直角。
如果内部缺陷严重地按超声波声束定向,就认为其边缘和探头的轴在第一个底波的信号振幅降低到6dB的那一点上重合。测绘完内部缺陷的边缘后,测定其平行于和横向于轧制方向的最大尺寸。该尺寸的乘积被定义为缺陷的面积。